Hot Metal Desulphurization
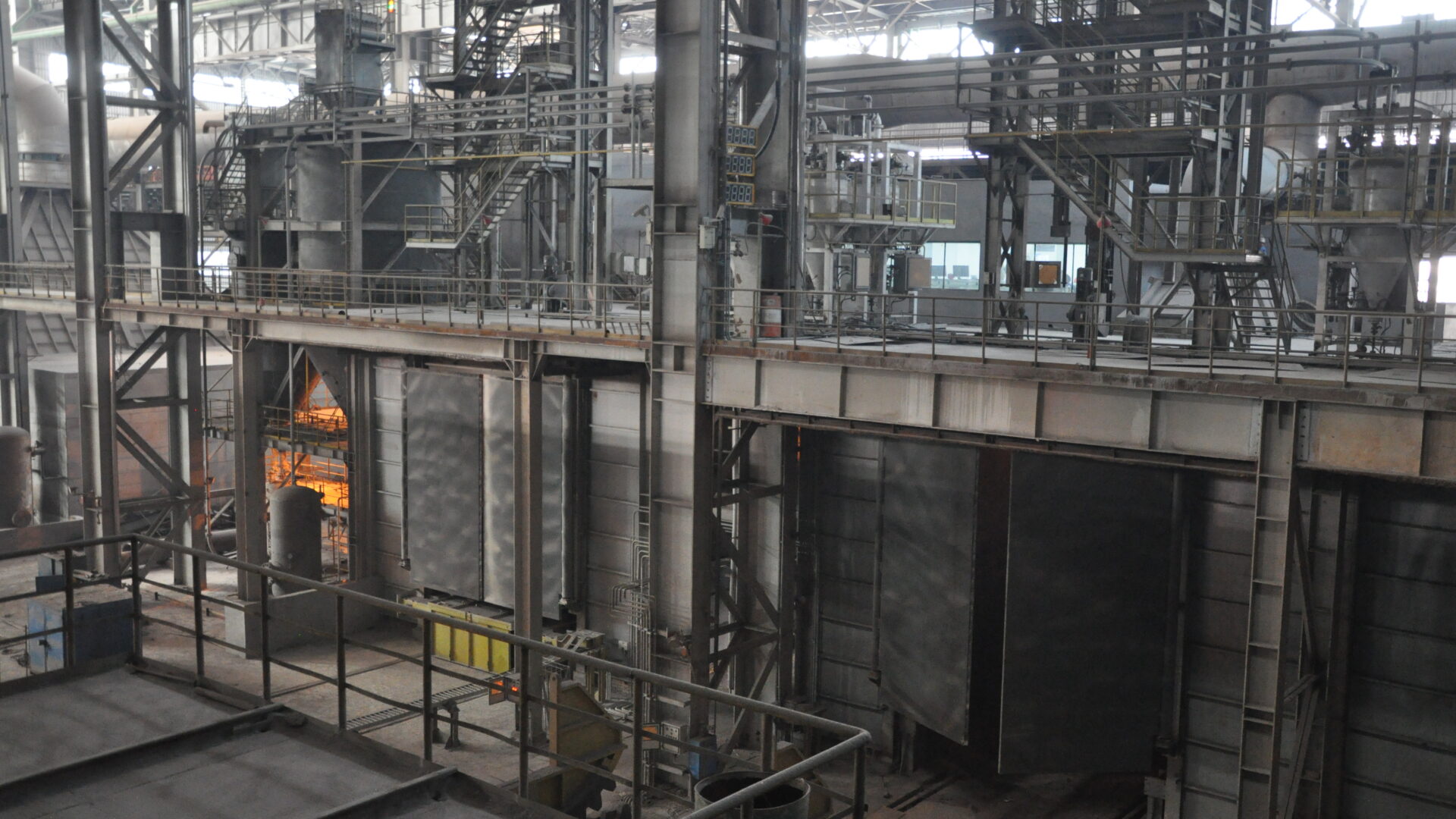
Hot metal desulphurization is the optimum solution for Sulphur control during steelmaking. Reagent materials are injected through a refractory lance into the hot metal transfer ladle, the most suitable vessel for hot metal desulphurization. The process model determines the reagent requirements and predicts temperature and iron loss, based upon hot metal condition and final Sulphur level.
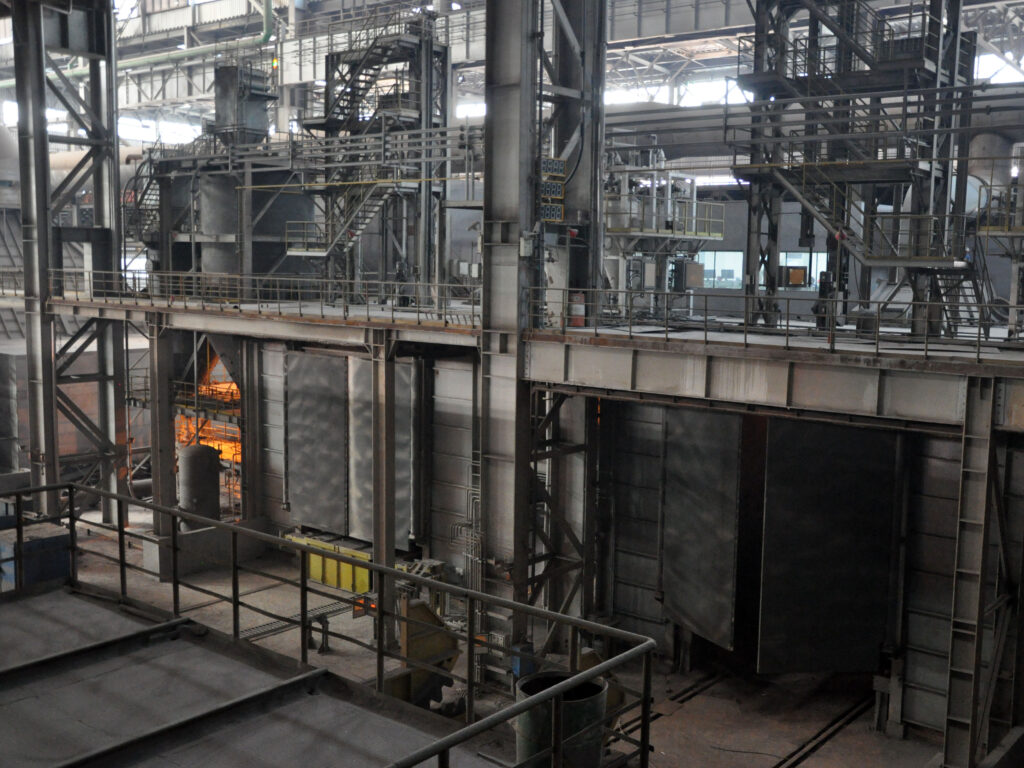
Flexible solution for co–injection
Hot metal desulphurization processes are primarily characterized by the injection method and the injected reagent. Chemical reactions for desulphurization with magnesium are 20 times as fast as the reactions when lime is applied.
For steel grades with low required sulphur content, lime is the preferred reagent, mostly injected through a rotary lance that injects sideways. This process ensures low final sulphur levels and limited turbulence, but processing times are long. When driven for plant output, magnesium injection entails a fast process, but equilibrium conditions have somewhat higher sulphur content in the bath.
The Danieli Corus co–injection can inject lime, calcium carbide and magnesium–either individually or combined. This brings the advantage of being able to achieve both quick and deep desulphurization depending on heat specifications using a single desulphurization station.
Resulphurization
When magnesium sulphide reaches the bath surface, it tends to resulphurize in the presence of oxygen. This effect can be detrimental for steel quality and needs to be prevented. Since magnesium sulphide takes relatively long to rise to the surface, halting the slag skimming operation further adds risk of resulphurization.
Sulphur can be bound using calcium to form the more stable calcium sulphide. The used calcium source may either be lime or calcium carbide. Co–injection is an ideal desulphurization method also in this respect.
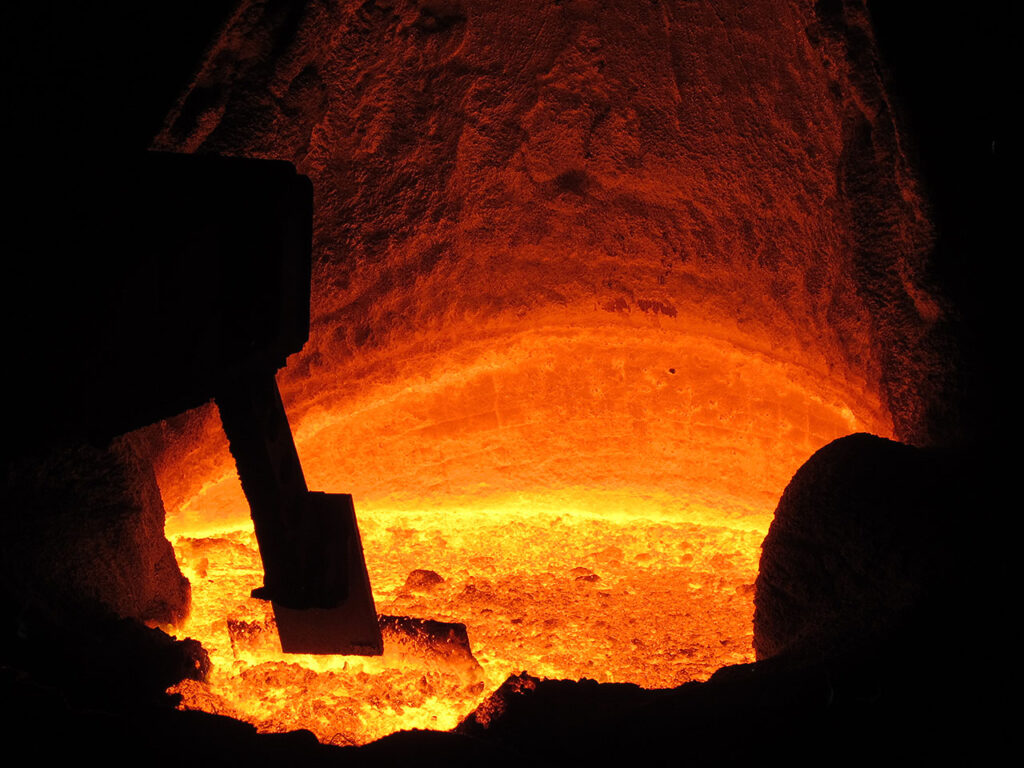
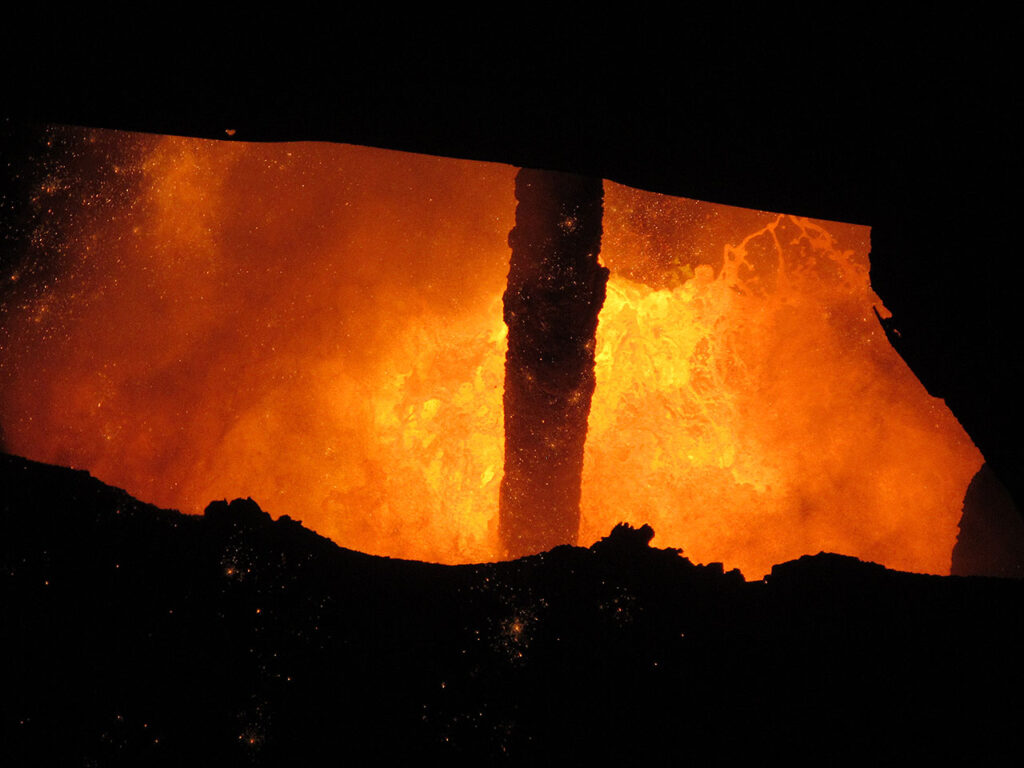
Process control system
The Danieli Corus process control system allows the operator to have ultimate control over the desulphurization process. The system includes tailor–made Level 2 software, which is equipped with a reliable metallurgical model and data reporting facilities.
The system has a user–friendly interface and interacts with Level 1 and Level 3 systems continuously. The model provides the highest possible hit rates, while minimizing costs. Thanks to the advanced model and high level of automation of the Danieli Corus Level 2 system, fully automatic desulphurization operation at the push of a single button is possible.
References
63
Largest vessel size
300 t
Hot metal desulphurization through co–injection of reagents is the most flexible solution, offering the possibility to do deep as well as quick desulphurization using a single station. In addition, the co–injection process has the lowest cost for iron loss, equipment wear and temperature loss.
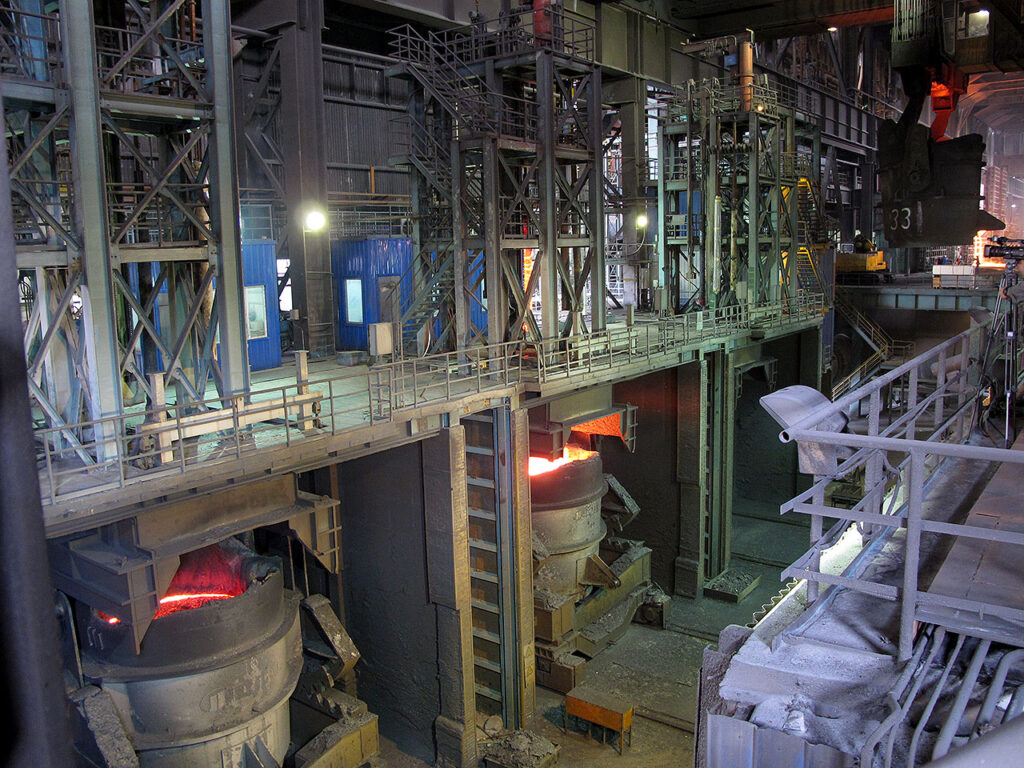
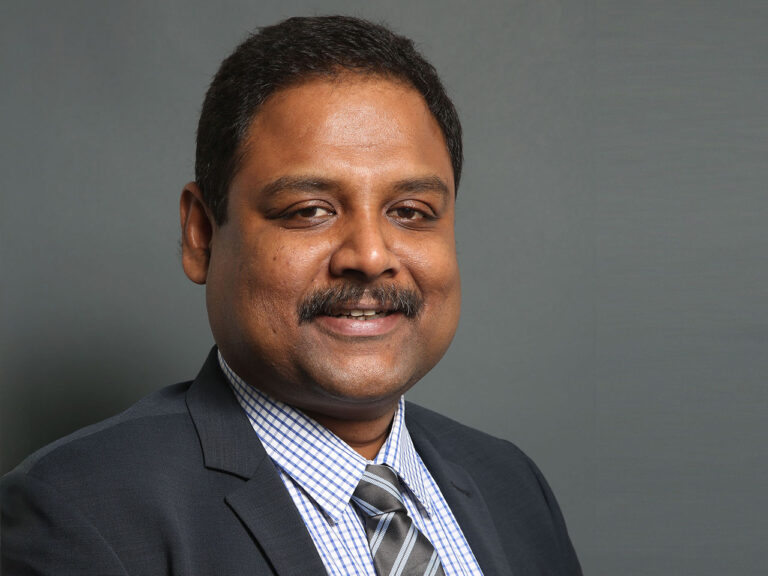