Intelligent Steelmaking with AutoTAP

AutoTAP is an automation package designed to fully automate the tapping sequence of the BOF Converter. AutoTAP employs state–of–the–art automation, sensors and cameras. The technology utilizes existing systems to their full extent to safely automate the full tapping sequence in the BOF Shop. AutoTAP is an essential step towards “no man on the converter floor”.
Key benefits of AutoTAP technology are the following:
- Fully automated tapping preparation and operation
- Minimum operator interference
- Automated ladle car movement
- “Single button”, fully automatic control from the start of the tapping sequence until converter uprighting
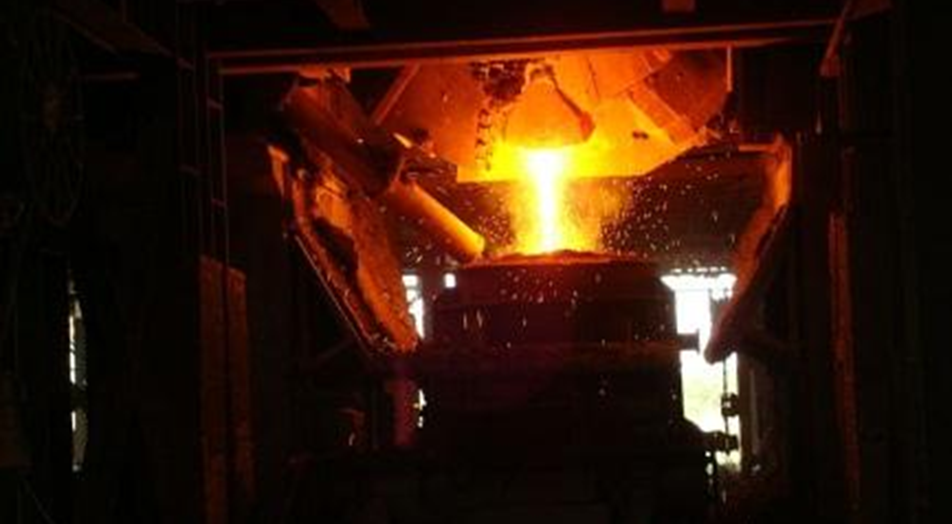
Tapping process automatization
The AutoTAP system strongly improves converter tapping time consistency and ladle transfer car positioning. Movement of the ladle transfer car does not require any manual intervention, eliminating delays in ladle arrival. The technology reduces spillage during tapping while increasing productivity.
Slag carryover reduction
Implementing AutoTAP leads to a significantly improved tapping practice, reducing slag carryover by up to 15%. This reduction brings a host of benefits: alloying yield increases, directly lowering alloying costs, while aluminium recovery improves—making aluminium usage more efficient and cost–effective. Having fewer aluminium inclusions enhances product quality. In the Ladle Furnace, processing times for lime removal are shortened, the need for deslagging is reduced, and process efficiency improves. For critical steel grades, phosphorus reversal decreases, minimizing grade diversions and sequence changes at the continuous caster. Additionally, the refractory life in the ladle’s slag zone is extended.
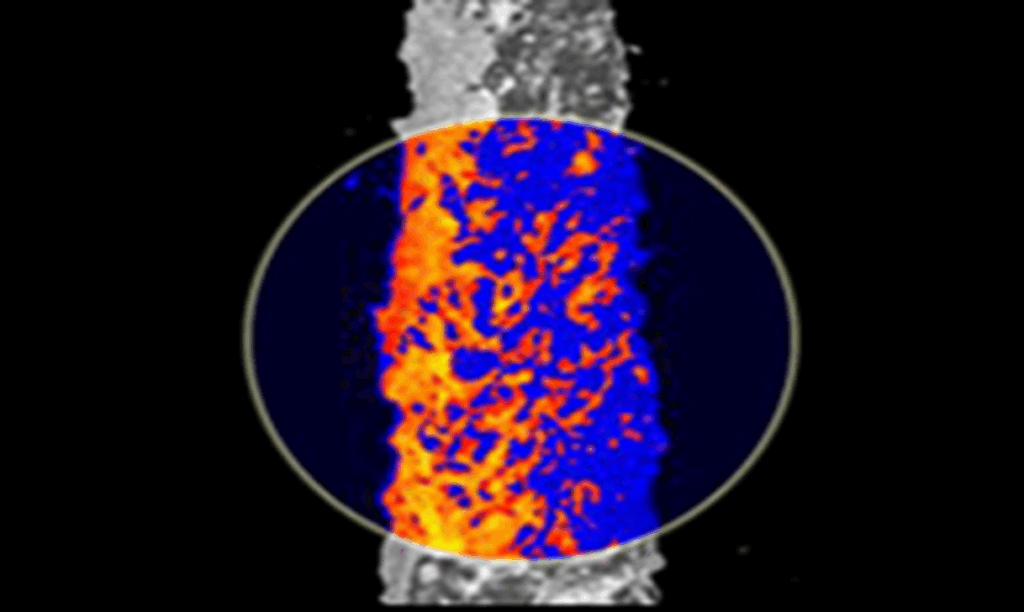
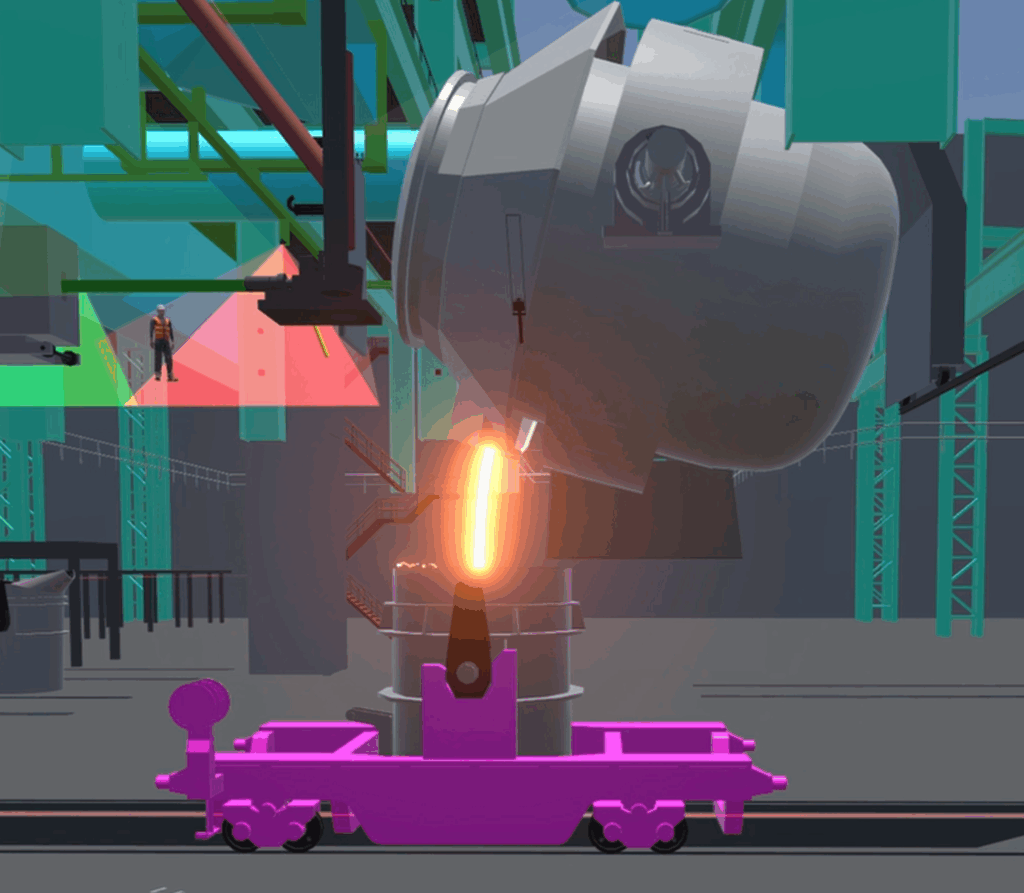
Safe working conditions
AutoTAP significantly enhances shop floor safety by minimizing the need for human intervention during tapping operations. The system proactively issues alerts and warnings, advising personnel to stay clear of the tapping floor while in operation. A key feature is the integration of a customized fail-safe application, SafeBOF, which prevents operational mishaps and ensures safe, incident–free shutdowns of the AutoTAP system. To boost reliability, all critical components are designed with redundancy in mind.
Moreover, AutoTAP includes a digital twin—an advanced simulation tool that supports operator training and allows for scenario-based optimization in response to process changes.
Slag Carryover Reduction
15 %
Alloying yield improvement
2 %
Tapping time reduction
3 min
Implementation at Shagang
The first implementation of AutoTAP technology was completed at one of the BOF Shops at Jiangsu Shagang Group’s Zhangjiagang plant. For Shagang, who are China’s largest steel producer in the private sector, this project brought the envisaged improvements, marking a major step forward in automatic steel production.
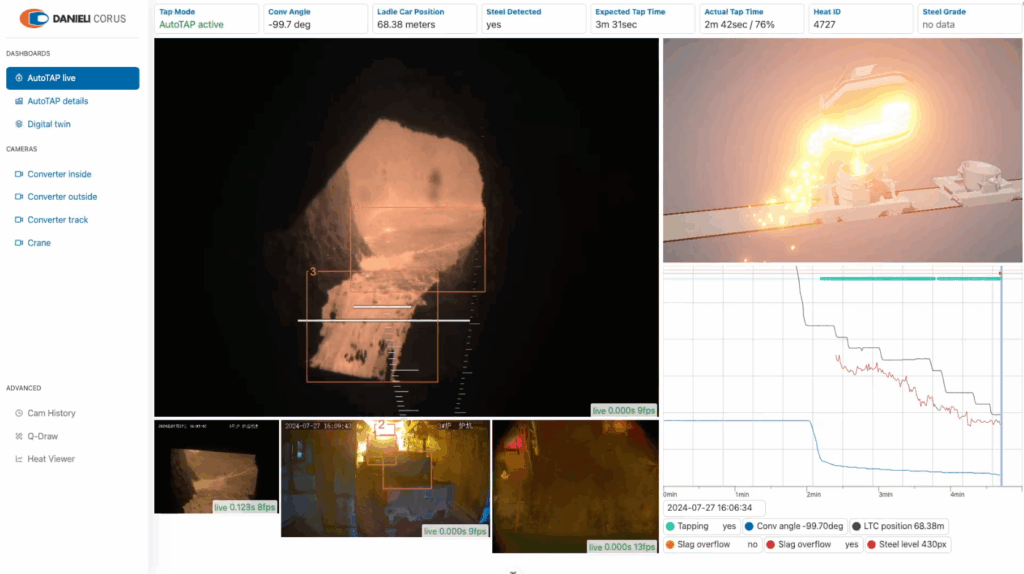
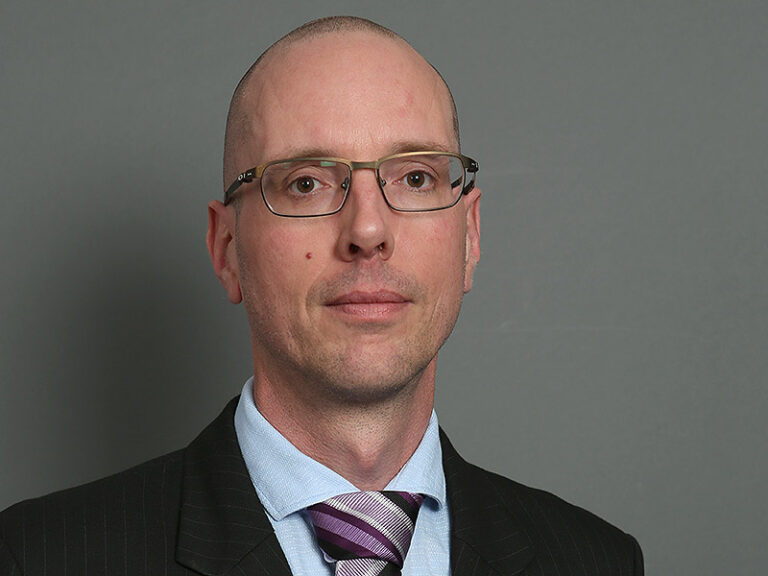