Tuyere Injection Systems
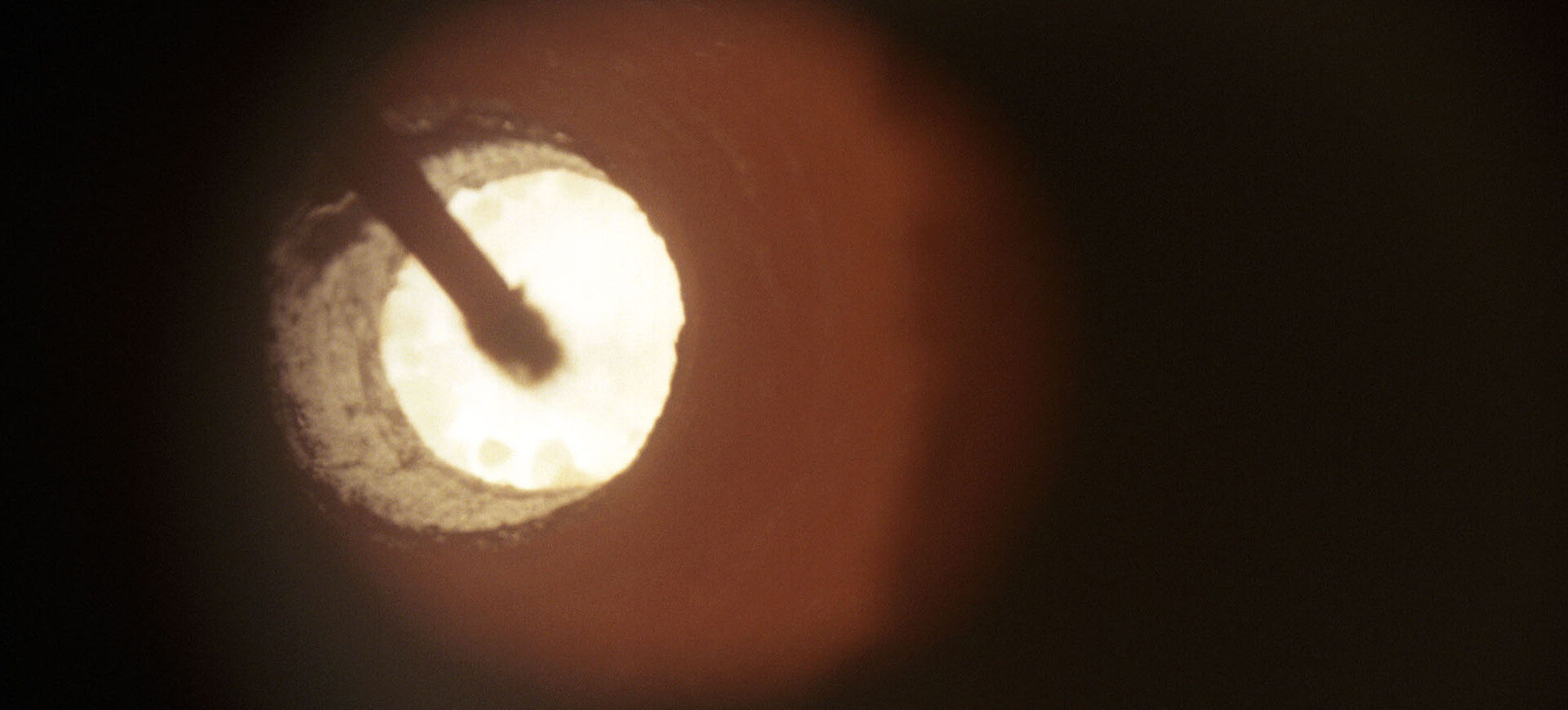
Today’s requirement for CO2 emission reduction leads to an increased focus on hydrogen–rich gases for injection into the tuyeres in addition to the fully matured practice of pulverized coal injection. Examples of hydrogen–rich injection gases are natural gas and coke oven gas. Where coal injection and natural gas injection are straightforward, coke oven gas needs to be compressed in relative costly equipment. Danieli Corus offers tailor–made solutions for the injection of solids and gases. Via in–house CFD modeling and software simulations, advise for the best process-and equipment solution is available with our experts.
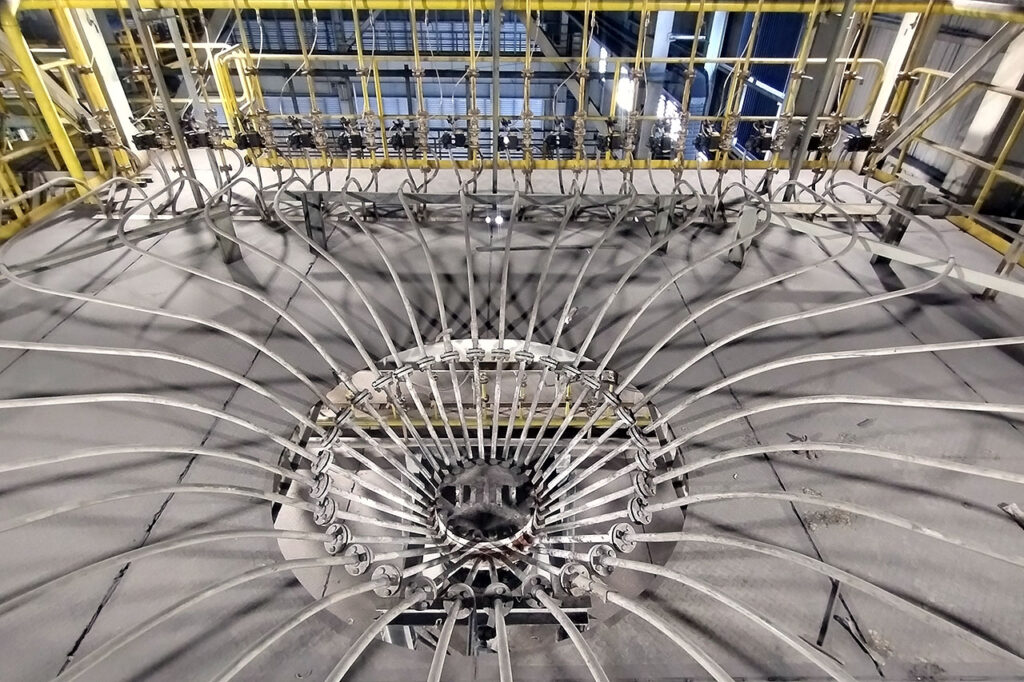
Equal distribution, low gas comsumption, highest availability and injection rates
Our injection systems ensure uniform coal distribution across tuyeres by applying equal pressure drop across all injection lines using straightforward physical principles. This way, coal-to-gas ratios are exceptionally consistent and stable. Our dense–phase design minimizes gas consumption, while minimizing the presence of moving parts in contact with abrasive coal to maximize availability. These systems achieve industry–leading injection rates over 200 kg/tHM, reducing coke consumption and allowing for increased furnace productivity. With robust design, low maintenance needs, and adaptability to various injectants, our systems deliver a reliable, efficient, and high-performance solution for modern blast furnace operations.
Injection practice optimization based on global experience
With more than 200 operational assistance projects completed successfully, our blast furnace ironmaking experts have ample experience in process optimization, tuyere injection stabilization and ramp–up. This global experience is a great support for process engineers and blast furnace operators when optimizing their injection practices—regardless of whether this is based on traditional processes or next–generation practices.
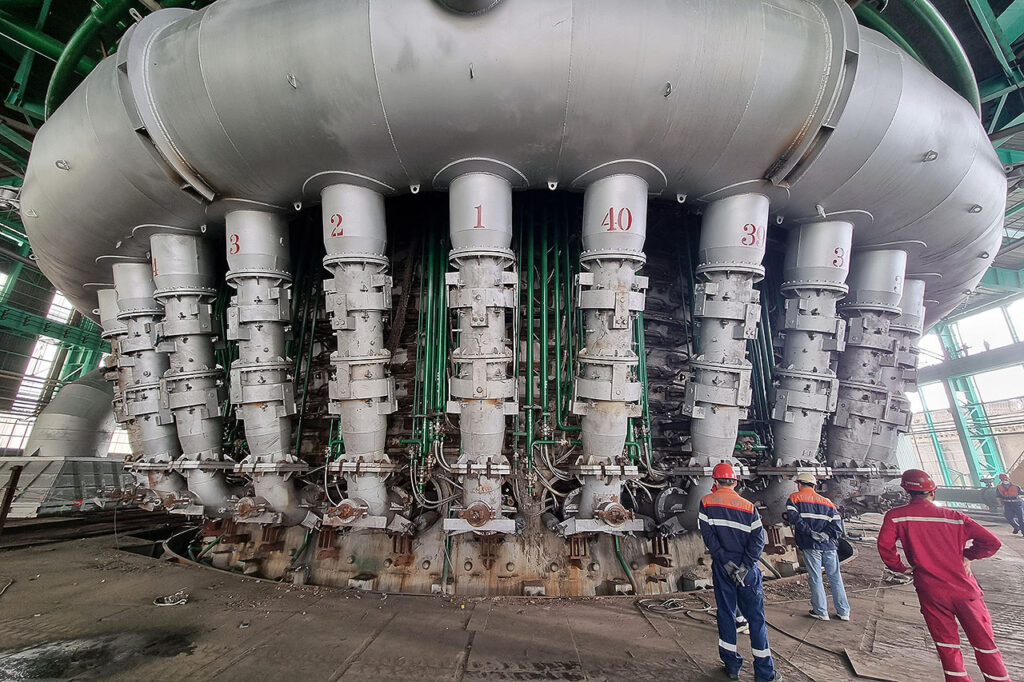
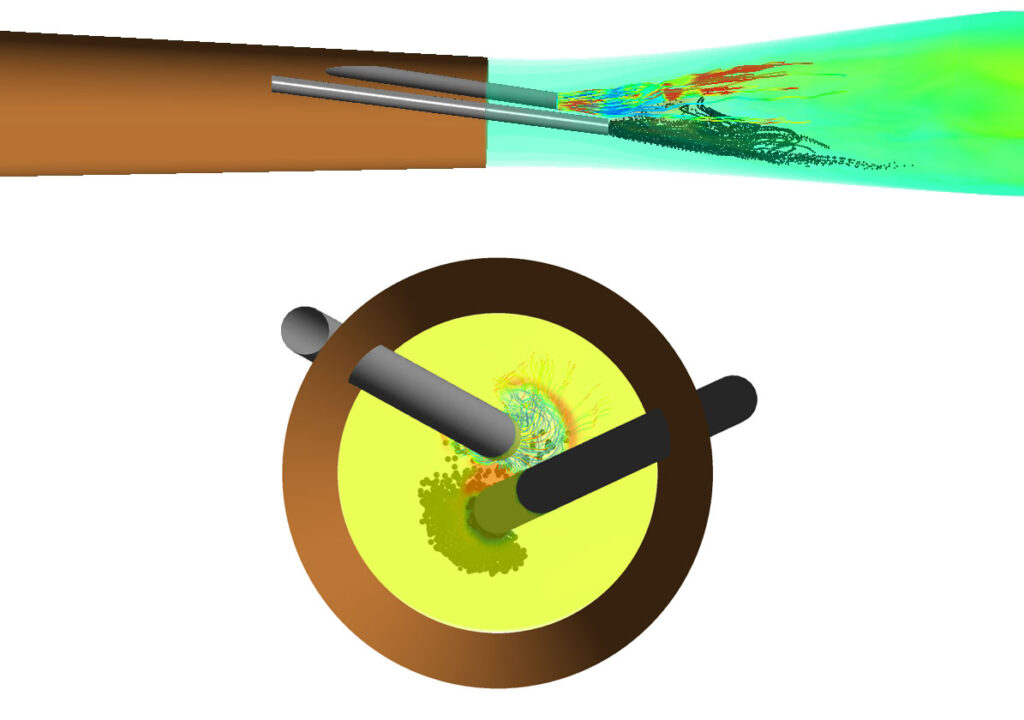
Process analyses for heat and mass balances and injection point optimization
With our proprietary, advanced mass and heat balance models for the blast furnace process, we evaluate operational setpoints as well as performance parameters for any tuyere injection scenario. CFD analysis, which we complete in–house, offers additional possibilities for assessing gasification and other phenomena taking place in front of the tuyere. Pre–assessments of optimum lance positions is particularly valuable when exploring next–generation tuyere injection processes.
Featured references
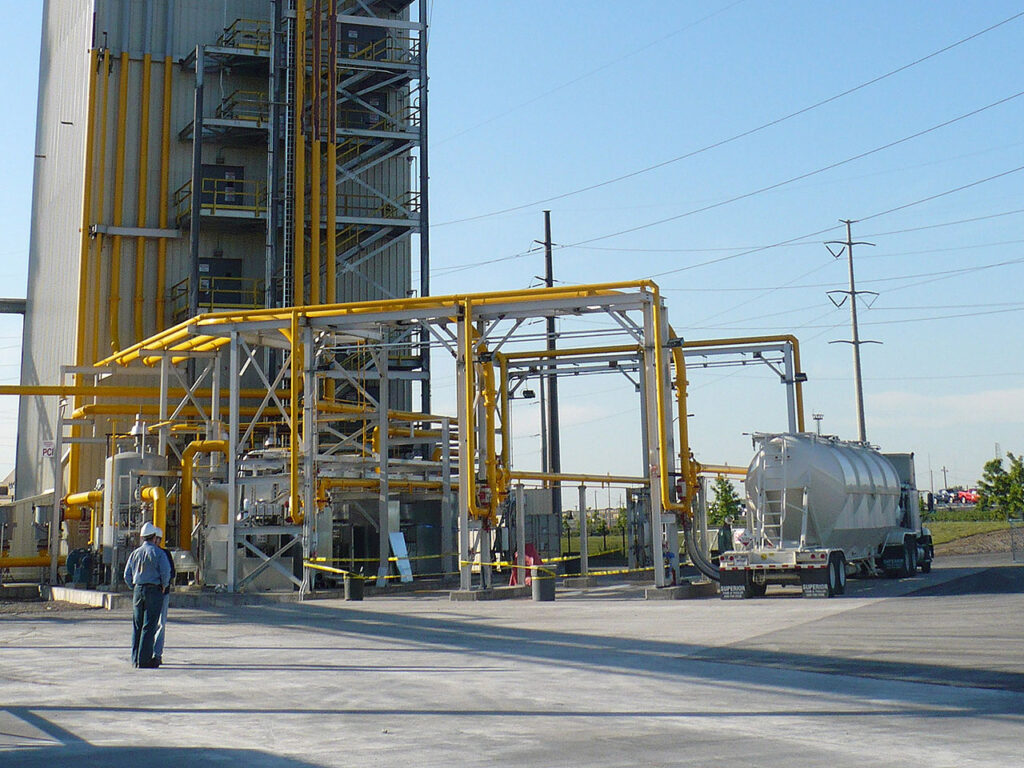
Pulverized Coal Injection System for Dearborn “C” Blast Furnace
Injection Systems
77
Record injection rates
270 kg/tHM
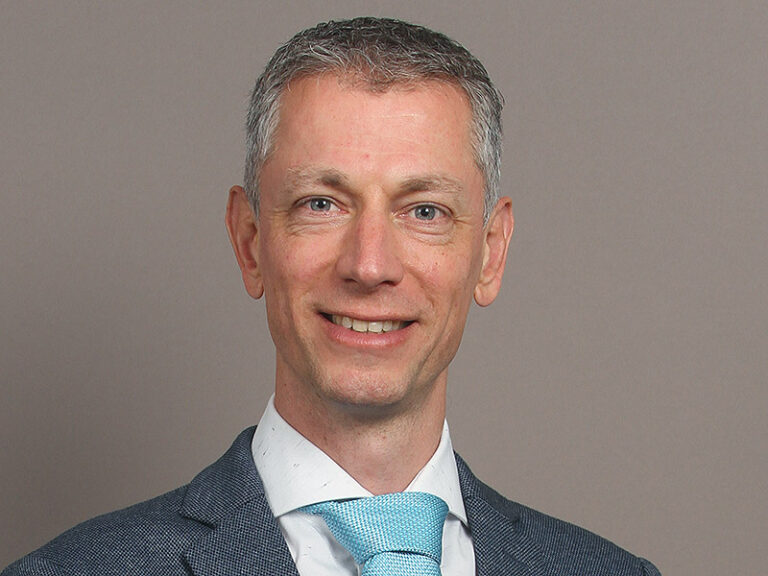