Gas Cleaning System
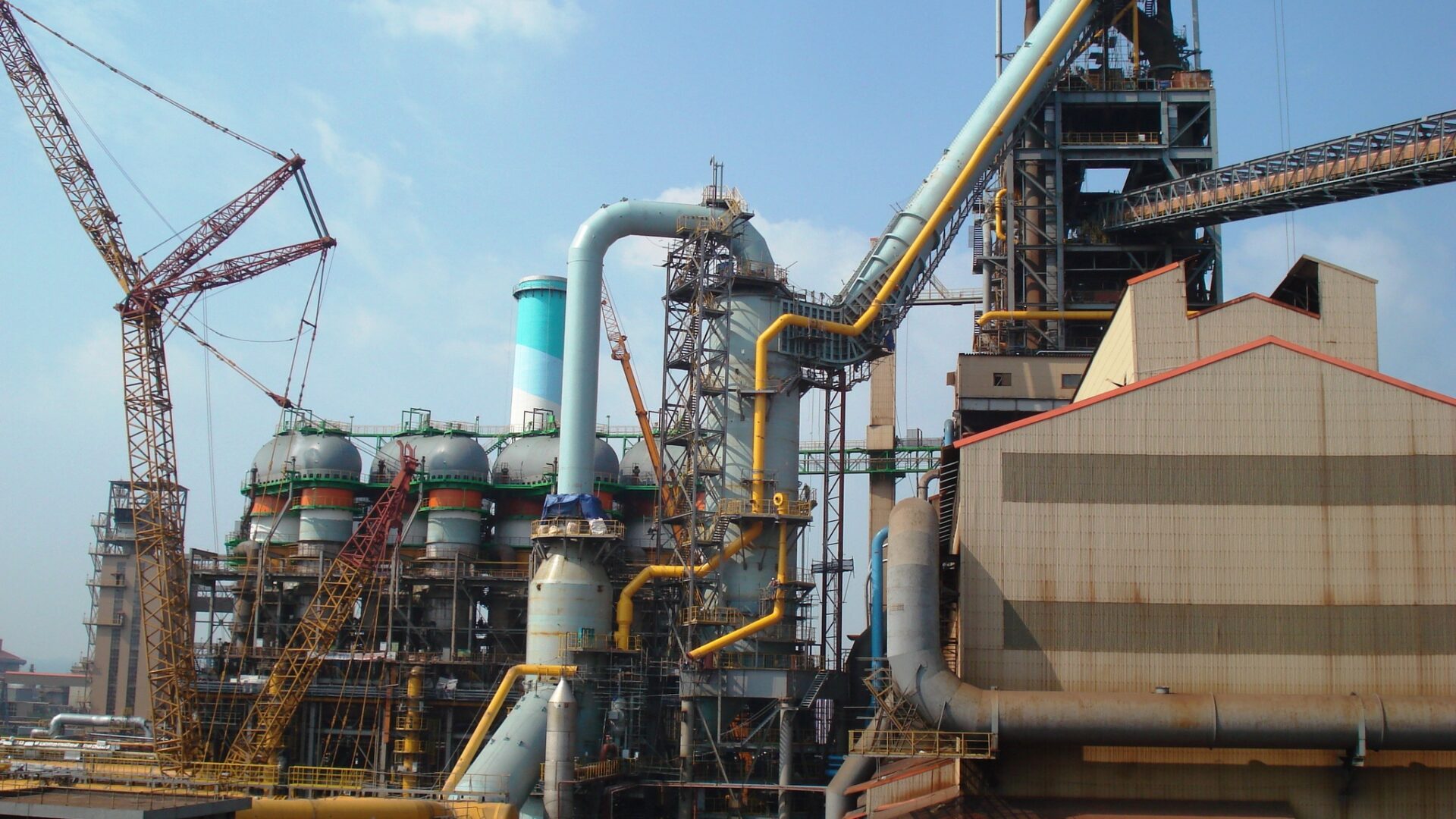
In order to use Blast Furnace gas as combustion or reduction gas, the gas needs to cleaned first. This requires the removal of solid and gaseous pollutants. The coarse dust, mostly consisting of iron oxide and carbon is first removed in a (cyclone) dust catcher. The fine dust particles and gaseous pollutant are removed in the second stage which could be a wet scrubber or a dry scrubber. After the two gas cleaning steps, the gas can be used as combustion or reduction gas elsewhere in the plant and the combustion products can be emitted without harming the environment.
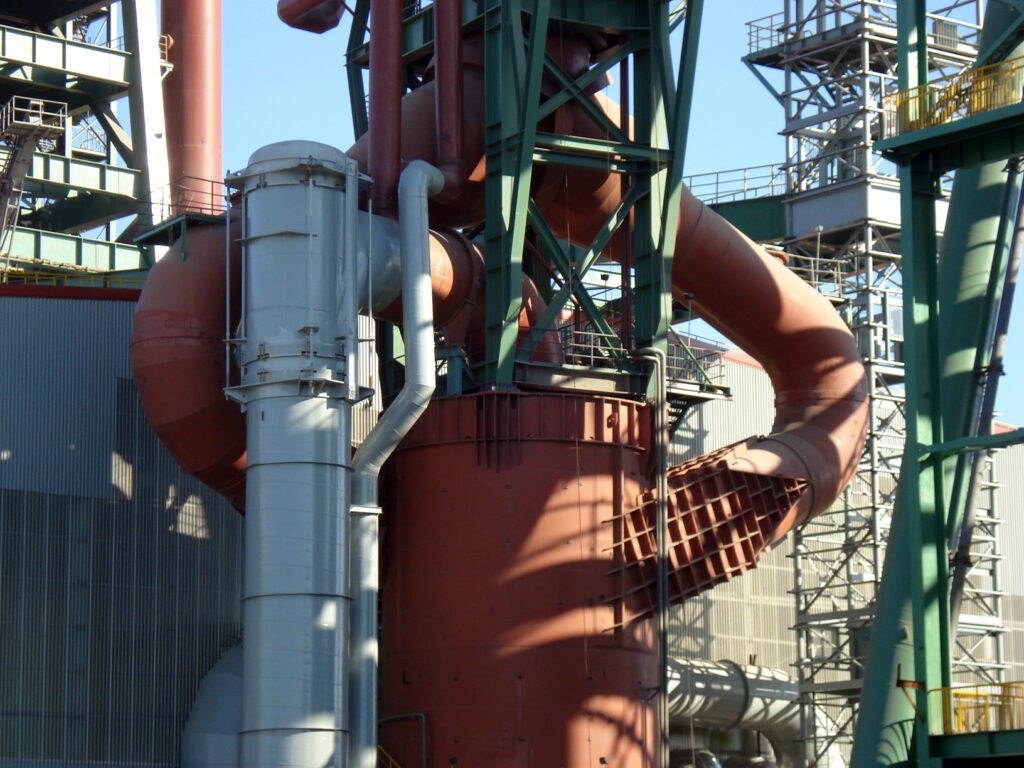
Efficient cyclone dustcatcher
The introduction of cyclone dustcatcher technology for the first stage of the blast furnace gas cleaning system greatly improved dust removal and recycling. Traditional, gravimetrical dustcatchers have a removal efficiency of around 50%, whereas cyclone dustcatchers can be engineered for dust removal efficiencies of around 85%. Since the balance of the dust carried over to the second scrubbing phase is rich in zinc, this represents a reduction in waste dust that needs to be processed otherwise from 50% to 15% of the total amount.
Danieli Corus promotes tangential cyclones, with axial cyclones offered as an alternative in case of e.g. space restrictions. Tangential cyclones—either single or dual inlet—have the great advantage of the absence of wear–prone parts such as inlet vanes.
Proven dry second stage
Dry gas cleaning eliminates the consumption of high volumes of scrubbing water, which is a great advantage in areas with water scarcity. Not having to process this scrubbing water in turn eliminates the requirement for an effluent treatment plant, reducing the system’s total footprint. Finally, a dry second stage improves the quality of the blast furnace gas in terms of temperature, pressure an calorific value—substantially increasing the output of the turbine. With many references in dry scrubbing technology for the primary aluminium industry, the Danieli Corus system is the only proven option offered to steel producers.
The applied Pleno V technology has the following unique features:
- Conditioning tower that protects the bag filters in case of temperature spikes—the only design with proven “dry bottom” operation, preventing downstream acidic corrosion and scaling
- Patented VRI reactor for reagent injection
- Bag filter modules using low pressure pulse–cleaning for longer bag life and smaller baghouse footprint
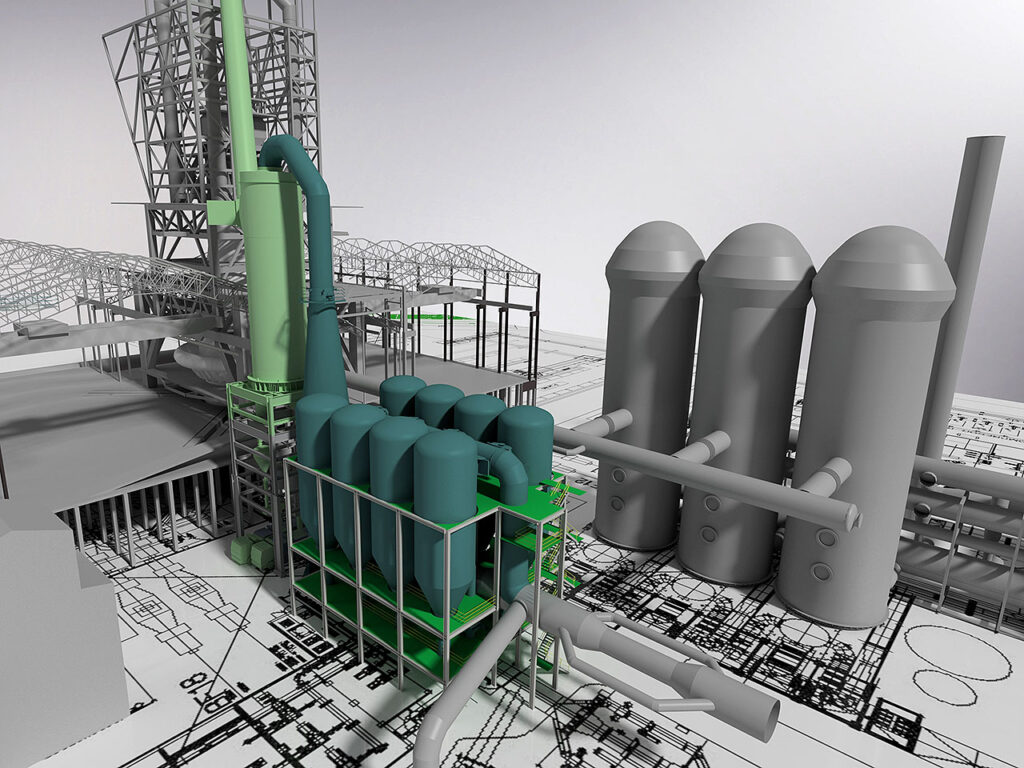
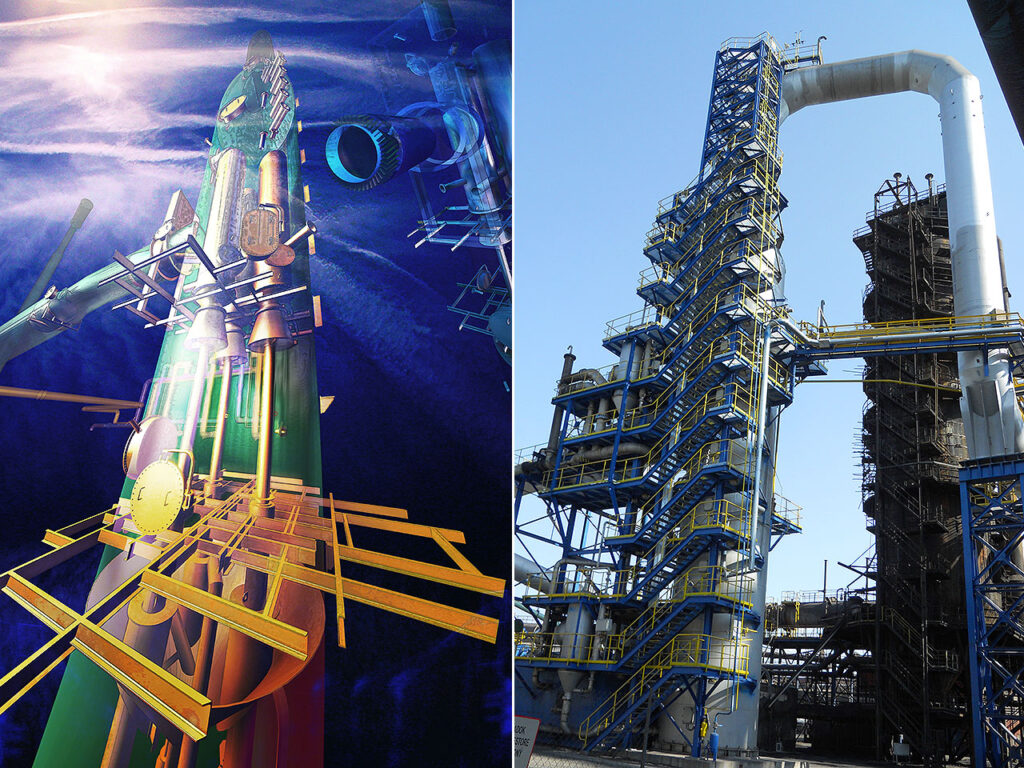
Wet second stage
Wet scrubbers can also be used. Such scrubbers consist of an initial pre–scrubbing part and two or three annular gap elements where the fumes are humidified and cleaned respectively.
The pre–scrubbing part already removes a large portion of the (coarse) dust and ensures 100% humidity of the gas entering the second stage.
The annular gap elements consisting of a stationary top part and a moving bottom part, creates a very intense contact between the blast furnace gas and the sprayed water. The annular gap parts are made from casted stainless steel and are extremely wear resistant.
Recycle of the water from the second scrubbing stage to the first scrubbing stage, saves a lot of water and pump energy.
Next–generation mist eliminator
In wet gas cleaning systems, a mist eliminator is required downstream of the scrubber to remove droplet carry–over. Danieli Corus has developed a patented mist eliminator for blast furnace wet gas cleaning that achieves exceptional separation efficiency. Traditional axial types reduce free moisture from 250 to 4–5 g/Nm³ (~99.6% efficiency). This new design, proven in the oil and gas industry, lowers moisture content to below 0.1 g/Nm³—an industry benchmark of 99.96% efficiency. The design relies on three stages of droplet removal:
- Shell SchoepentoeterTM diverter inlet for coarser droplets
- Sulzer MellachevronTM vane type mist eliminator using droplet inertia
- Sulzer KnitmeshTM coagulator with an additional MellachevronTM step
The key advantage of this very high droplet removal efficiency is the prevention of corrosion caused by droplets that may collect at the bottom of the hot blast stove burner, lower energy losses as less droplets need to be evaporated and finally the prevention of combustion problems and draining issues.
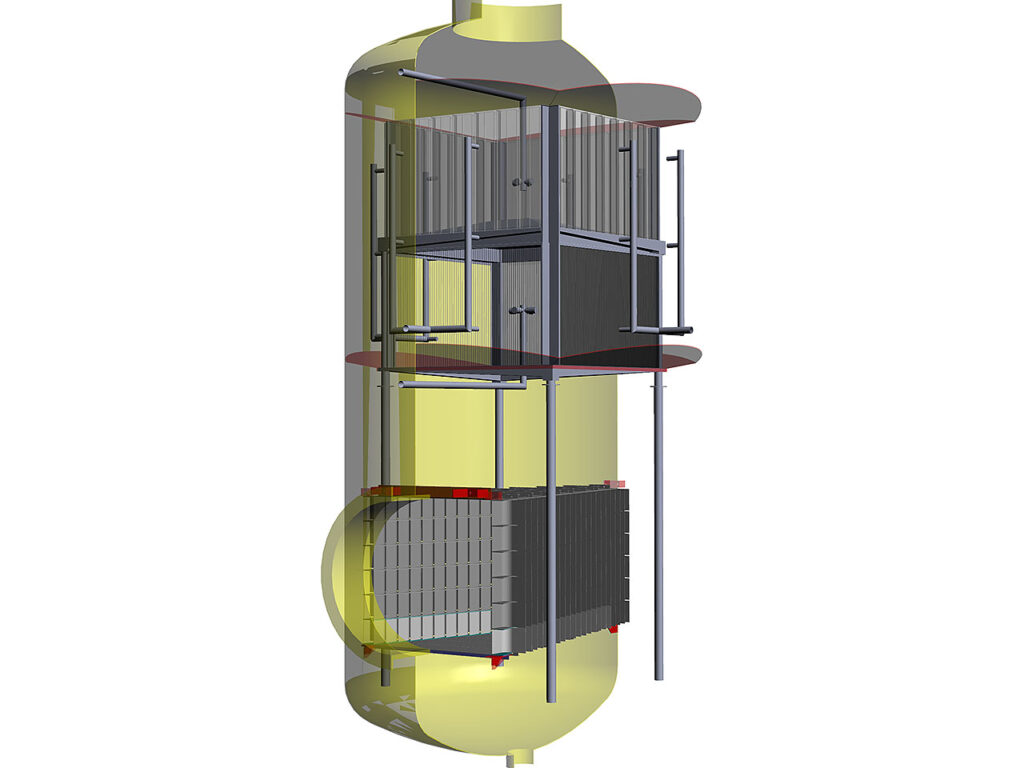
Projects
50
Cyclone dustcatchers
16
Dry gas cleaning systems
3
In both existing and greenfield situations, Danieli Corus gas cleaning systems are tailored to meet your environmental, operational and environmental goals. Whether your challenge is a complicated tie–in into an existing plot plan, demanding specifications for the clean gas or water scarcity, our engineering specialists are fully geared to develop a fitting solution at optimized Capex and Opex.
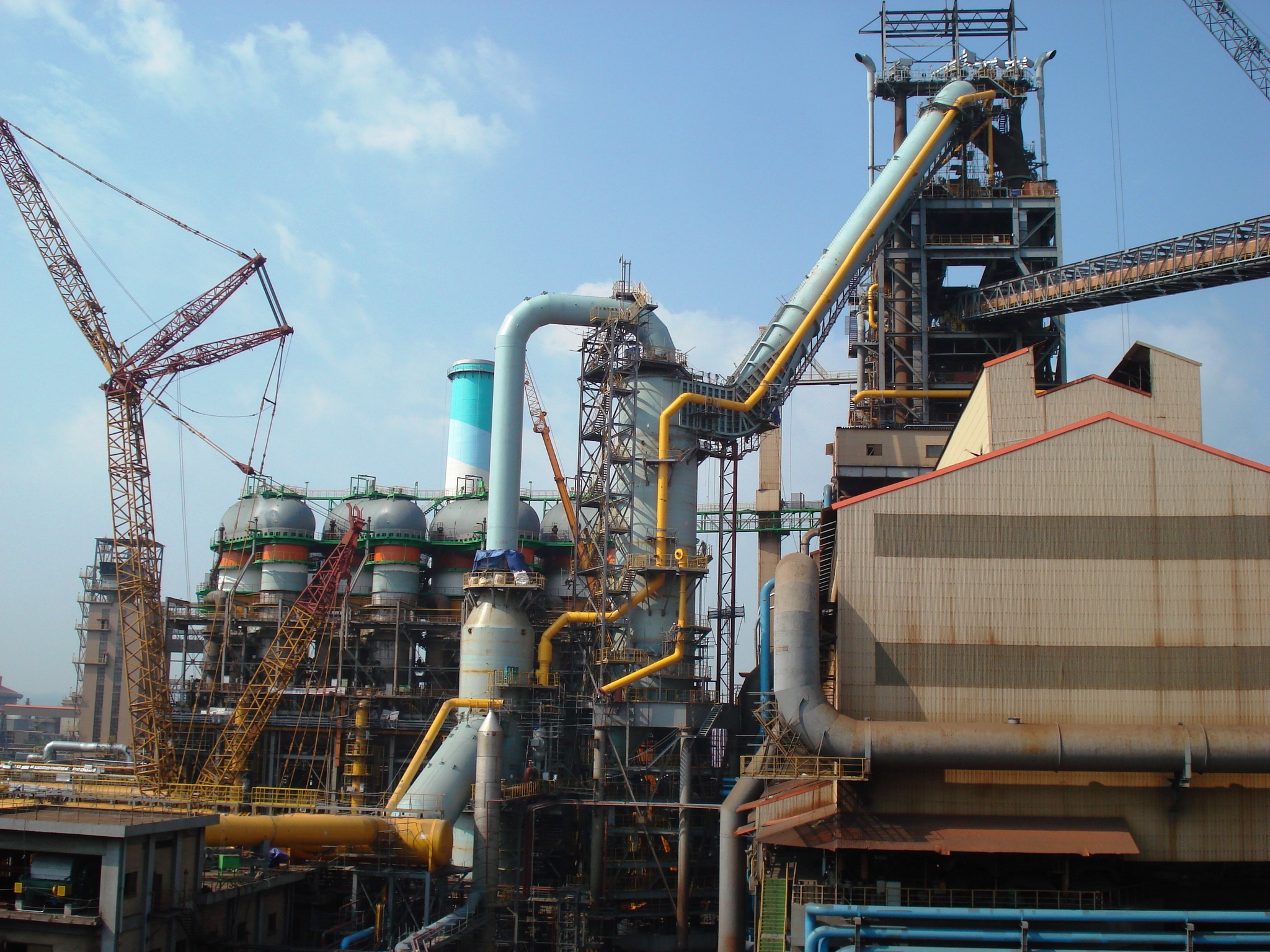
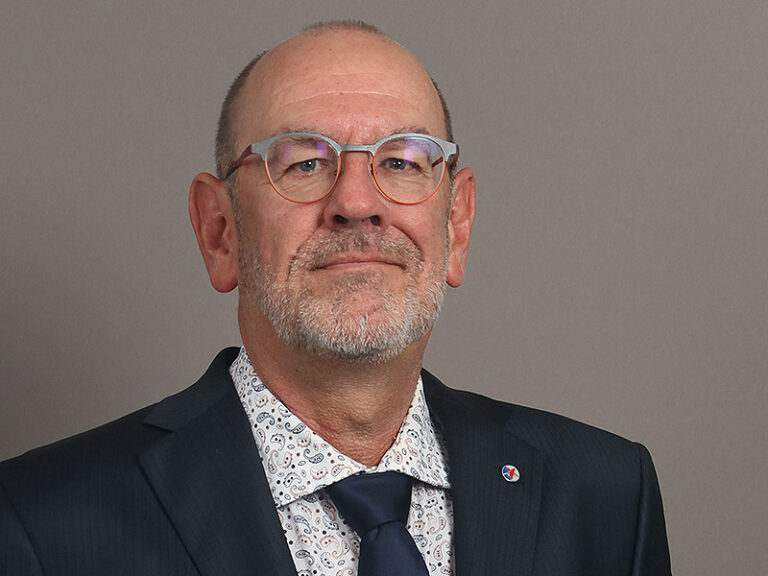