Blast Furnace Cooling and Lining Design
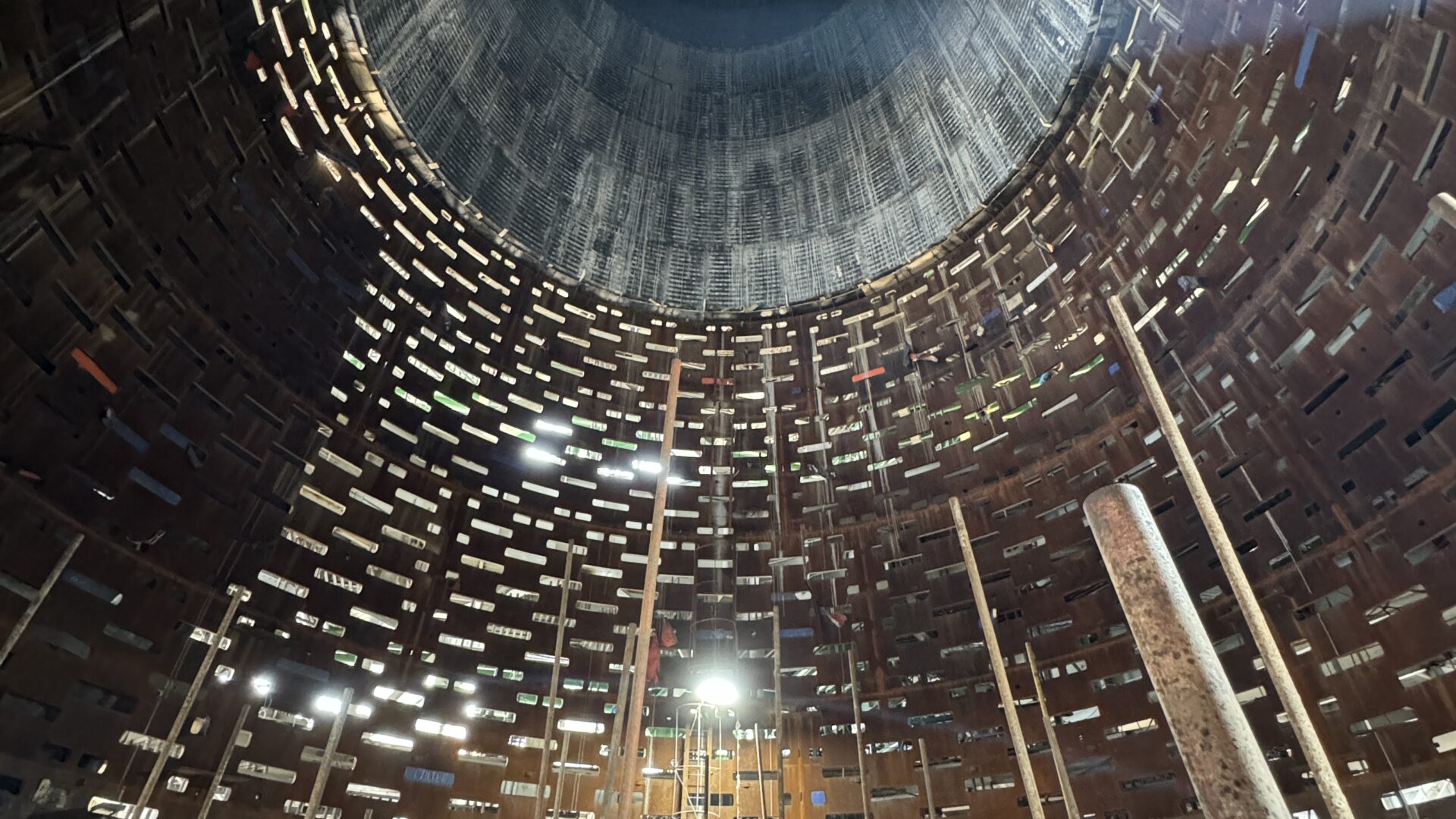
The “Hoogovens” integrated blast furnace cooling and lining design promoted by Danieli Corus is the only design, of which the capability to achieve long and safe campaigns under all process conditions is beyond debate. The combination of a dense pattern of copper plate coolers and high–conductivity graphite refractories is the most effective in creating and sustaining a skull accretion layer that protects against thermal, chemical and mechanical attack. Some steelmakers have designated this design “the indestructible bosh”.
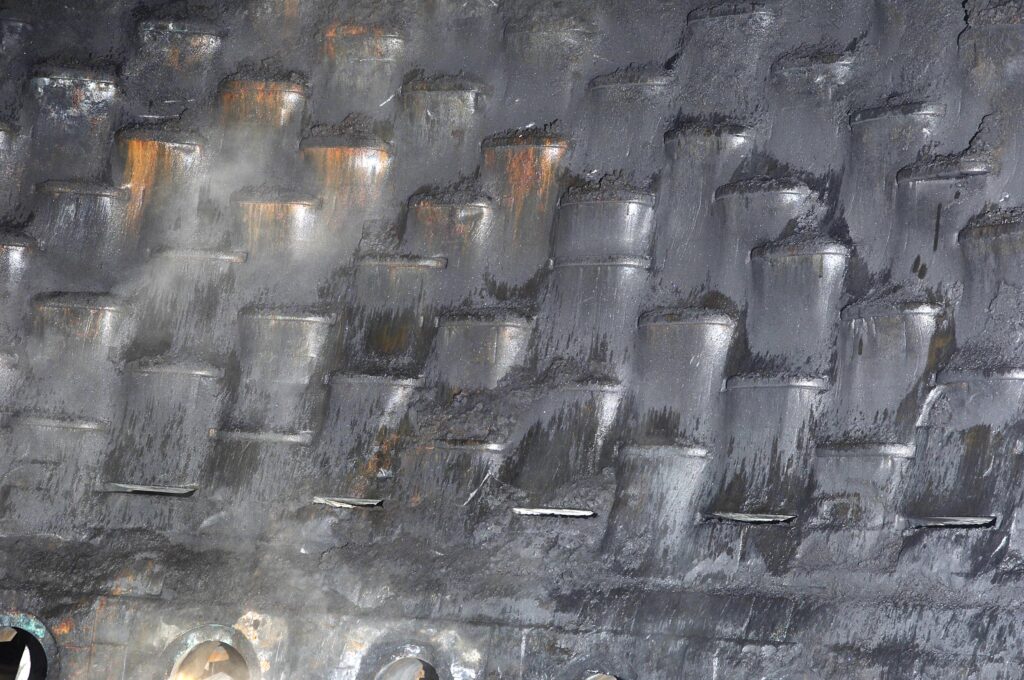
Long lifetime
Achieving a long and uninterrupted blast furnace campaign is not simply a technical achievement, it is a strategic advantage in terms of plant performance and profitability. Firstly, avoiding unnecessary relines defers major capital expenditure over the entire lifetime of the plant. But more importantly, long campaigns allow for a far more secure implementation of plant strategies given the absence of uncertainty and the longer horizon.
Finally, when entering transition scenarios, for the blast furnace to be a secure supplier of hot metal and utilize its license to operate to the fullest helps make such scenarios a success.
High availability and reliability
A stable supply of hot metal to the BOF Shop stabilizes steelmaking operations, making it more cost–effective. This consistency is also beneficial for product quality, reduces process variability, and minimizes production delays. With fewer disruptions, energy and raw material usage become more efficient, enhancing overall plant productivity.
Reliable operation also further extends equipment life, lowers maintenance frequency, and reduces the risk of unplanned shutdowns. Eliminating these outages reduces overall maintenance expenditure and is beneficial for staff efficiency and well–being.
Ultimately, high furnace uptime translates to better asset utilization, lower operating costs, and a stronger return on investment—making it a cornerstone of competitive, high–performance steel production.
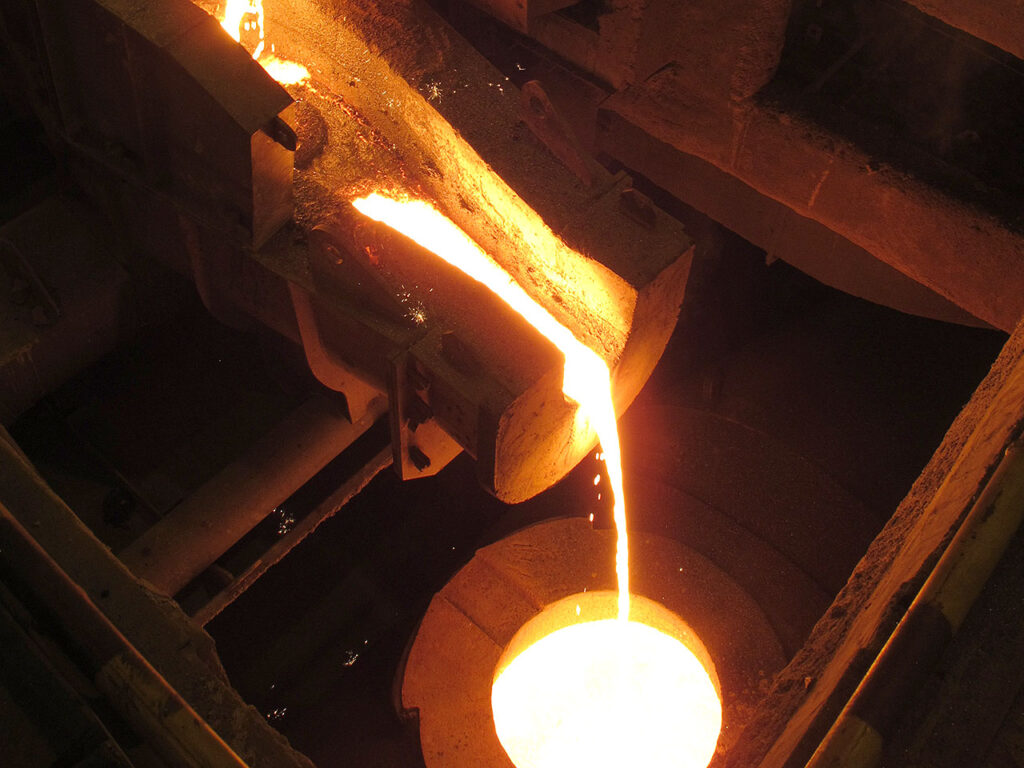
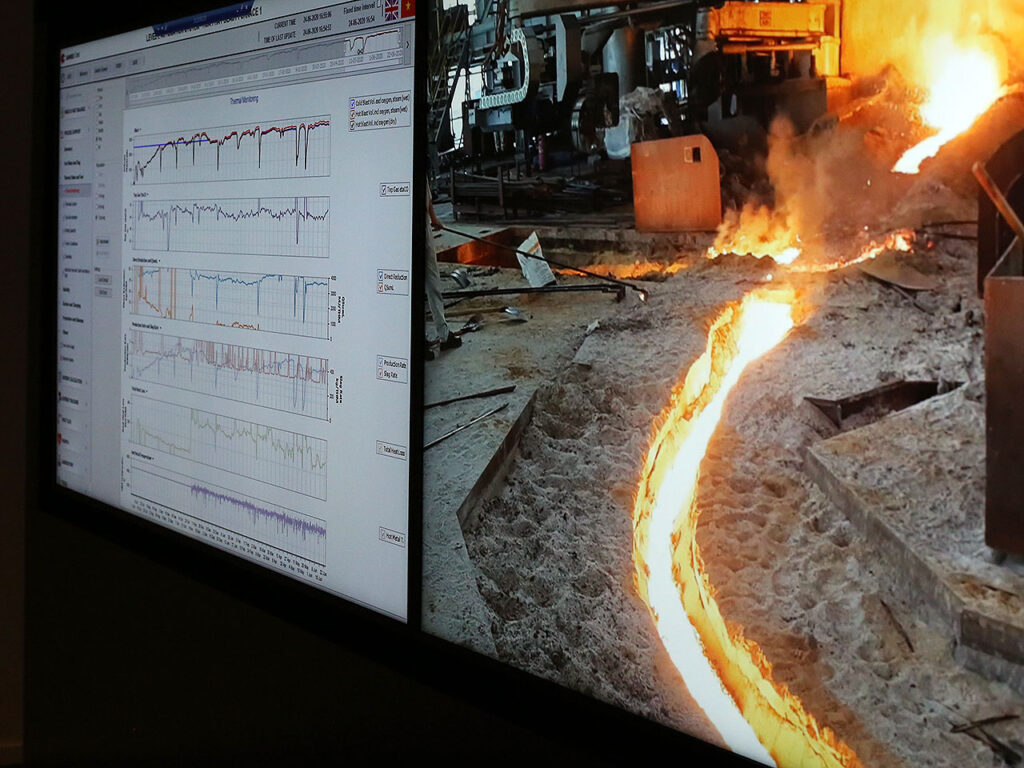
Modern instrumentation and automation
Modern instrumentation and automation systems improve process stability and efficiency, also contributing to longer equipment lifetimes. Real–time data regarding the process and equipment conditions helps the operator optimize the process and reduce detrimental effects for plant equipment. This not only leads to reduced fuel rates and emissions but also to more consistent hot metal quality.
An integrated process control system offers operating advice based on models that have been fine–tuned during implementation on all continents. Such systems deliver higher productivity, lower operating costs and improve operator effectiveness.
Featured references
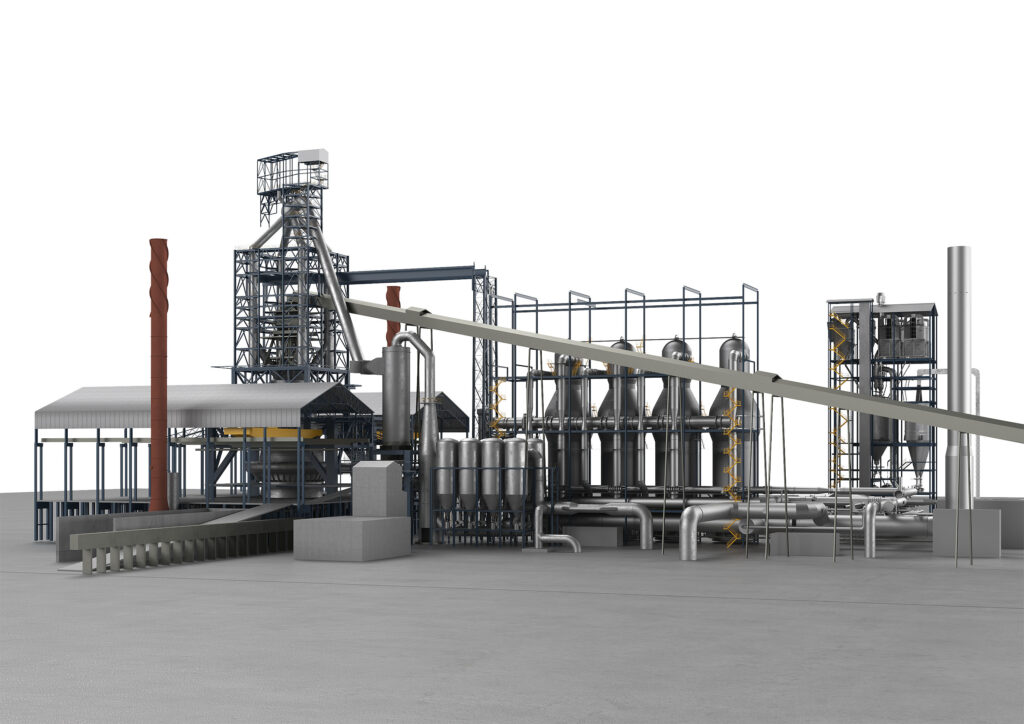
ArcelorMittal Nippon Steel India Greenfield Blast Furnace Nos. 2 & 3
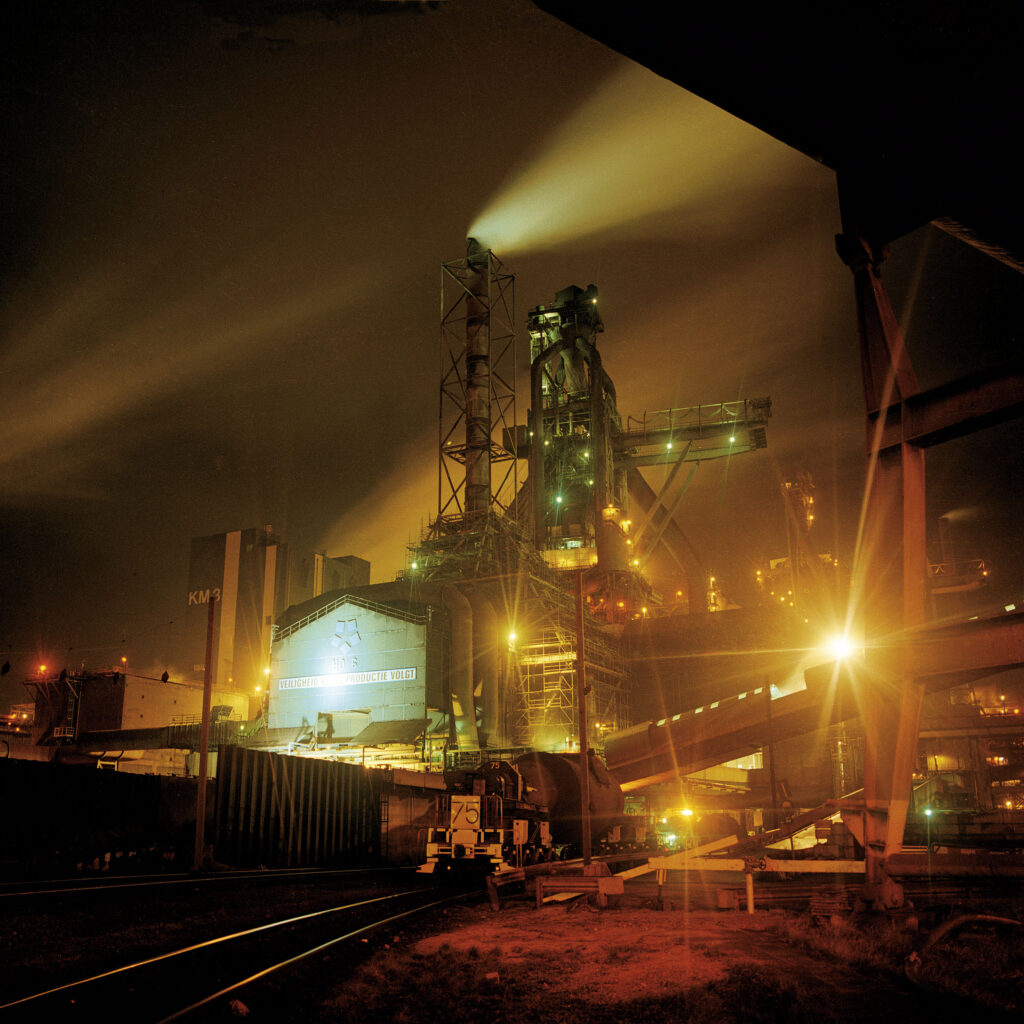
Tata Steel IJmuiden Blast Furnace No. 6
Projects
216
Maximum Inner Volume
6095 m³
Record campaign life
37 years
Record productivity
4 tHM/m³WV.d
A leading proposition
Our blast furnace cooling and lining technology is embraced by leading steel producers on all continents. The technology’s track record is undisputed as well as unparalleled, having set the following world records:
- The world’s largest blast furnace with a 6095 m³ inner volume
- The longest campaign life on records with 37 years
- The highest productivity in excess of 4 tHM/m³WV.d
- The highest levels of pulverized coal injection higher than 250 kg/tHM
The unique advantage of this technology is that none of these parameters are mutually exclusive: the furnace retains its ability to achieve a long and safe campaign even when operated at exceptionally high levels of productivity and/or fuel injection.
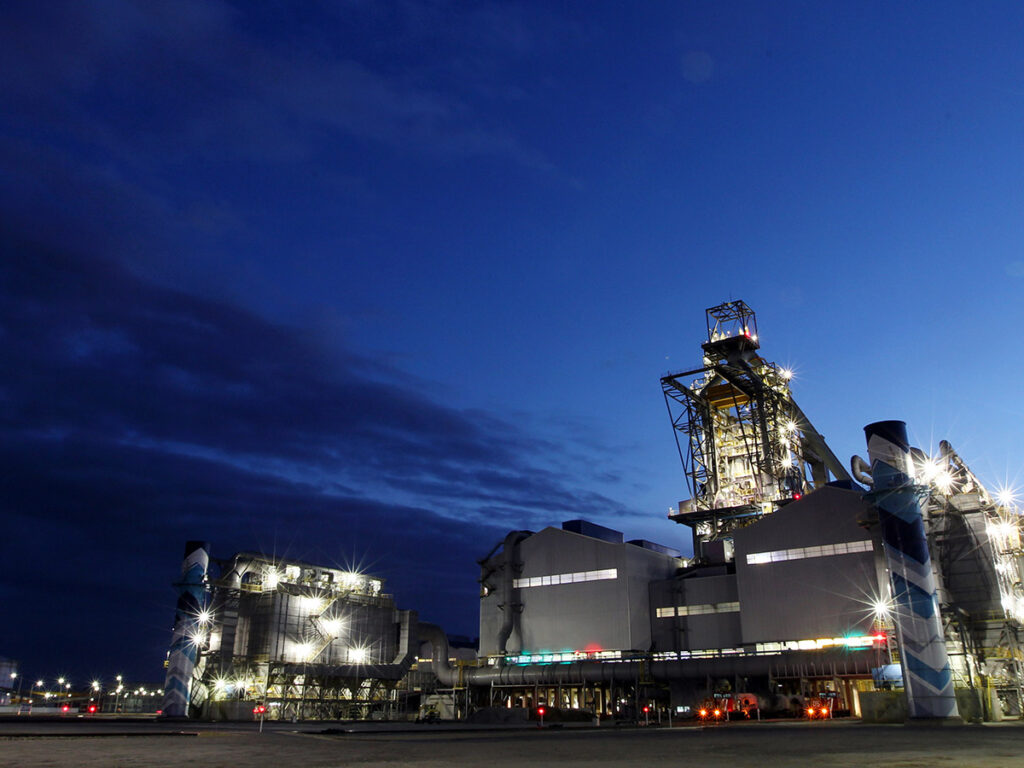
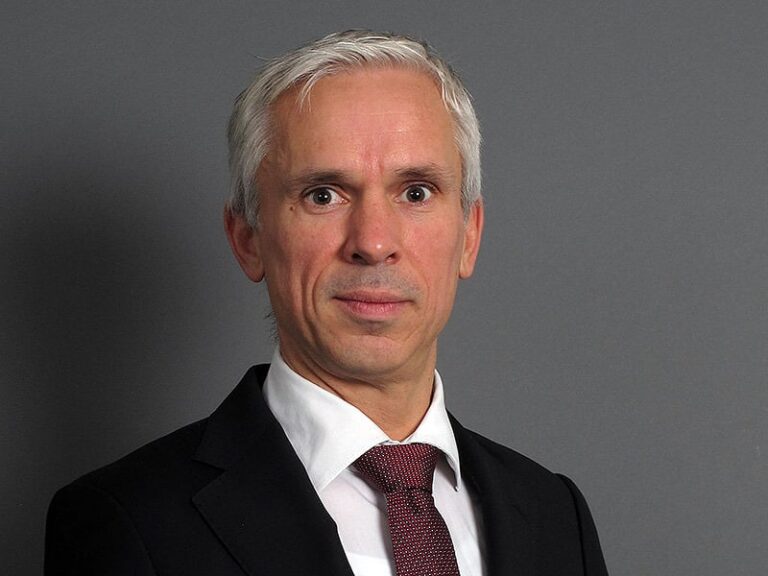