BF–BOF Steelmaking Decarbonization
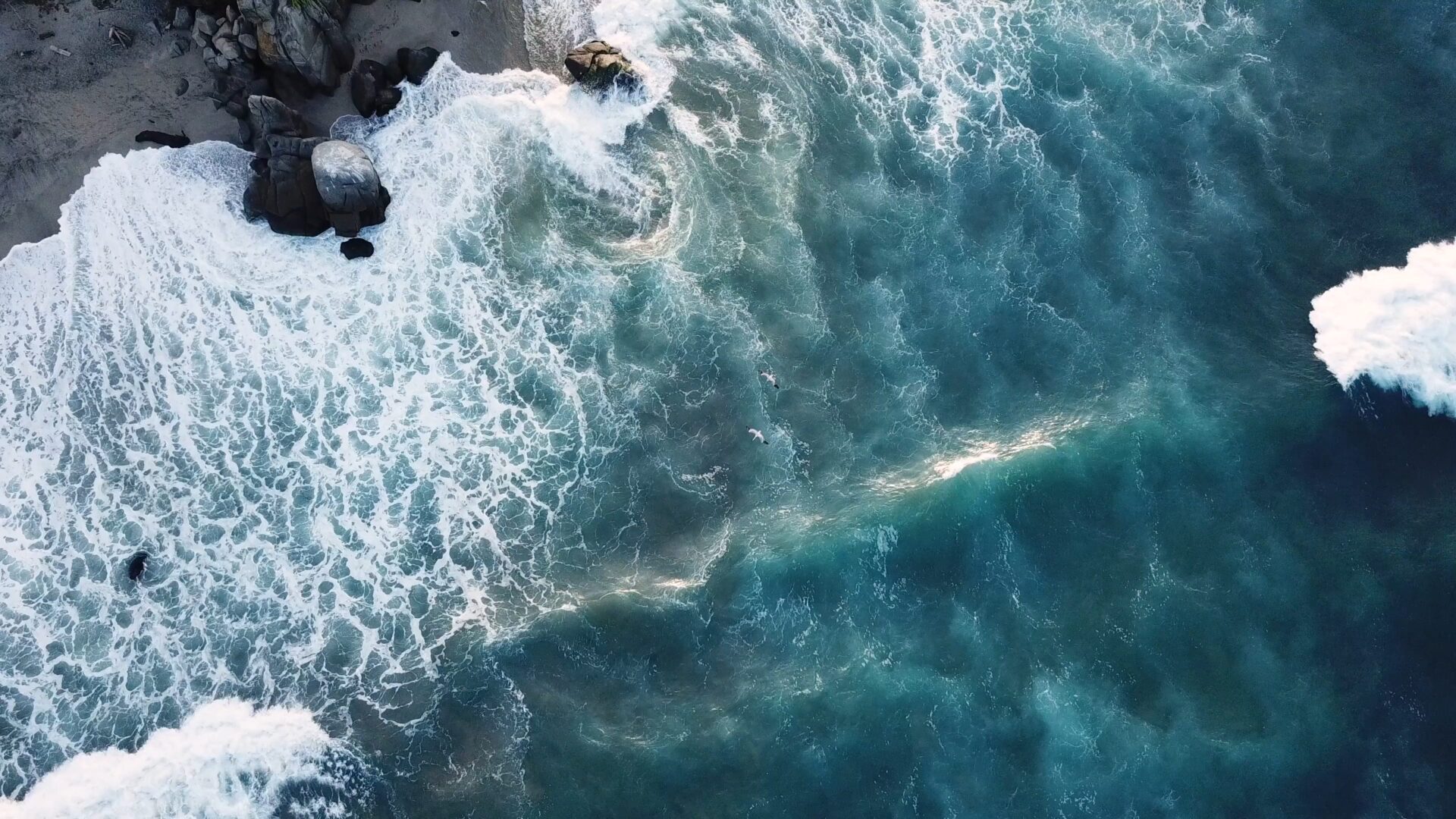
As the consequences of greenhouse gas emissions are becoming more and more evident, the urgency for our global industry to reduce these emissions cannot be underestimated. With steel production being accountable for 7–9% of global CO2 emissions, we have the responsibility to act now.
With their inherently favorable carbon footprints, Direct Reduction Ironmaking (DRI) and Electric Arc Furnace (EAF) Steelmaking are inevitably going to represent an increasing share in global steel production capacity over the next decades. Under many circumstances, however, the implementation of these greener production routes is unfavorable or even impossible. In many cases, lacking availability of e.g. scrap, green energy, natural gas and high–grade iron ores seriously undermines a business case. It is our responsibility to develop decarbonization options fit for risk–free implementation within every integrated steel plant.
a realistic scenario
We consider the DRI–EAF production route, using natural gas as a reduction gas in the Direct Reduction Plant (DRP), the base line for this decarbonization development. With its typical 40% lower CO2 emission in comparison to the traditional BF–BOF route, any further emission reduction inevitably requires partial or full transition to hydrogen–based DRI.
There is no environmental sustainability without financial sustainability
Any scenario that was considered for development has been assessed for its economic viability. Our mature industry has evolved towards its techno–financial equilibrium over the course of many years and any altered or hybrid configuration induces consequences in terms of CapEx and OpEx. Such consequences are partly or fully covered given the changed economic perspective that is part of the decarbonization paradigm shift—yet each and every scenario’s business case will have to demonstrate acceptable economics.
In order for our realistic scenario to be viable and allow for implementation tomorrow, it needs to overcome the challenges that steel producers are actually experiencing today as part of their evaluation of decarbonization options.
Our scenario addresses the following challenges.
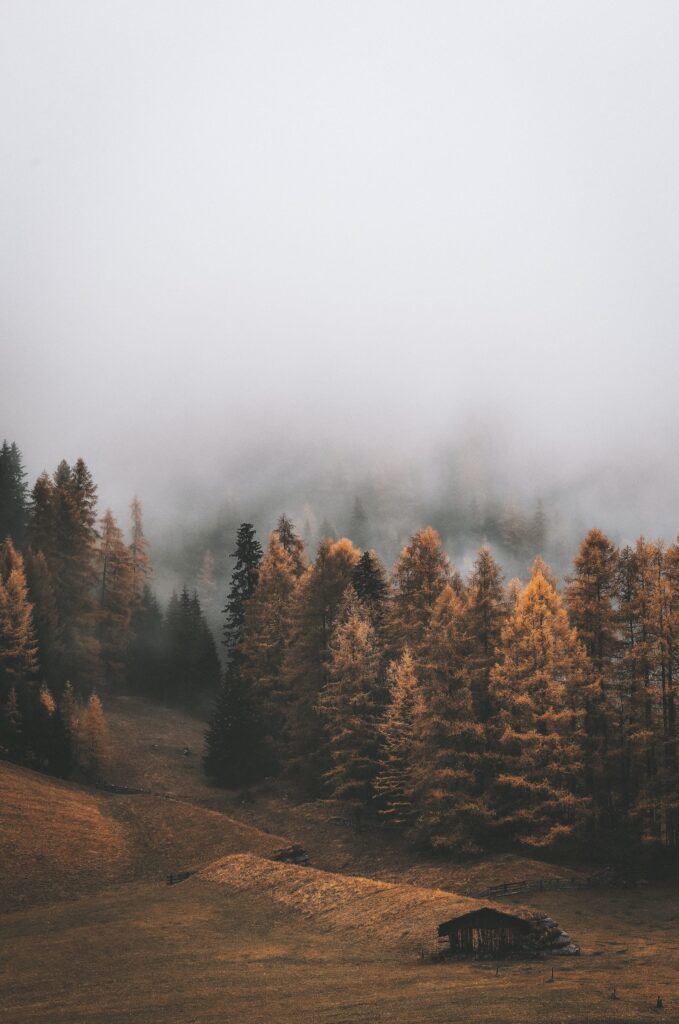
01 – ENERGY
Green electricity
Our assessments have demonstrated that many solutions presented to our industry depend highly on the availability of green electricity: in many cases, such scenarios only actually reduce CO2 emissions if grid carbon intensity is below 100 gCO2/kWh—which is only true for 1% of global steel production capacity.
02 – Hydrogen infrastructure
Lack of hydrogen
The application of hydrogen as a reducing gas is undeniably the holy grail of green steel. However, given the absence of infrastructure and elevated production cost we do not consider hydrogen a realistic option for decades to come.
03 – Raw materials
Availability of high–grade ores
With less than 10% of global iron ore shipments being acceptable as feedstock for Direct Reduction Ironmaking, the corresponding grades will become increasingly sought–after, further jeopardizing its afforability. In our realistic scenario, our plant configuration should be able to process every and any ore grade.
04 – Carbon capture and storage
Feasibility of CCUS
It is projected that by 2030, global Carbon Storage capacity will amount to approximately 1.25% of global CO2 emissions. In total, 1% of this capacity will be allocated to steel production, corresponding to roughly 0.2% of steelmaking CO2 emissions. Relying on the availability CCUS capacity represents an unacceptable risk.
05 – Technology readiness
Solutions with industrial references
Implementation of a technology that has yet to be proven or that needs to go through its scale–up phase is associated with risks that are in conflict with the objective of achieving the required emission reduction by 2030. A realistic scenario relies entirely on fully proven technology.
40% metallics in the BF
+
40% metallics in the BOF
=
40% lower Emissions
Charging elevated amounts of metallics such as scrap and DRI is a proven practice for both the Blast Furnace and the Basic Oxygen Furnace. Both cases require only very limited modifications to existing plant equipment, primarily relying on mature and solid process know–how and process control.
Also when accounting Scope 2 emissions of the (purchased) pre–reduced metallics, carbon footprint reduction is substantial.
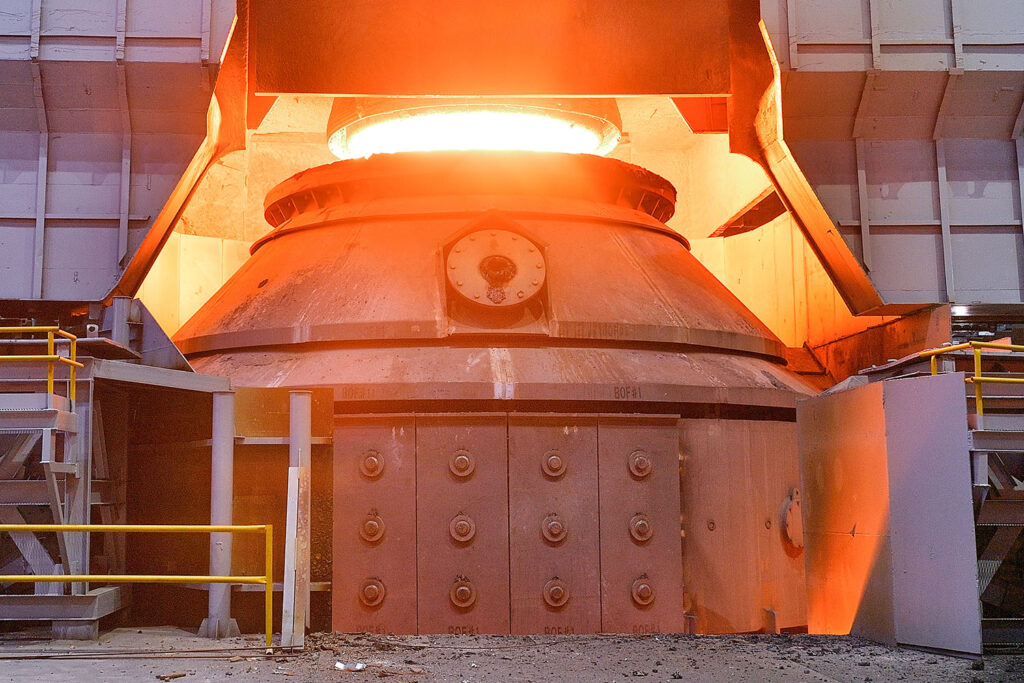
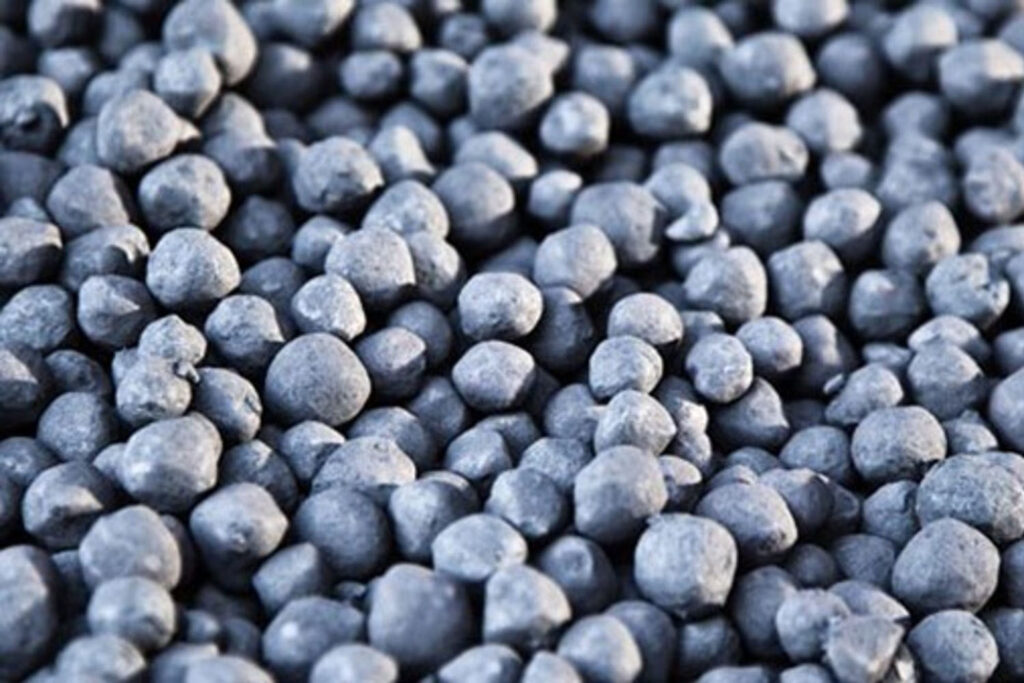
on–site dri production: hidden benefits
DRI is traditionally produced using natural gas to produce the reactor’s reducing gas, with a future shift towards hydrogen being inevitable. Implementation of a DRP within an integrated site also allows for the application of a mix of natural gas, coke oven gas.
This scenario represents an attractive re–allocation of coke oven gas. When compared to the base case of producing DRI using natural gas, specific CO2 emissions can be decreased by up to 17%.
Further Reduction Options
Raw Materials Pre–heating
Moisture, once inside the blast furnace, can be managed by for example increasing the fuel input or decreasing production rate. These measures, however, have a detrimental impact on cost and emissions. The optimum solution would be to eliminate the moisture before it enters the blast furnace in the first place—in the blast furnace stockhouse.
Coke Oven Gas Injection
The injection of hydrogen–rich coke oven gas into the blast furnace reduces the carbon rate and CO2 emissions as carbon (coke or coal) will be partially replaced by the hydrogen in the coke oven gas. Implementation is simple and cost–effective.
Bio–fuels
Using bio–fuels in the blast furnace significantly reduces fossil CO₂ emissions. Bio–fuels, such as bio–coal or charcoal, offer a renewable alternative compared to metallurgical coke or pulverized coal. When integrated effectively, they maintain furnace performance while enabling short–term emission cuts. Bio–fuels represent scalable step toward sustainable steelmaking.
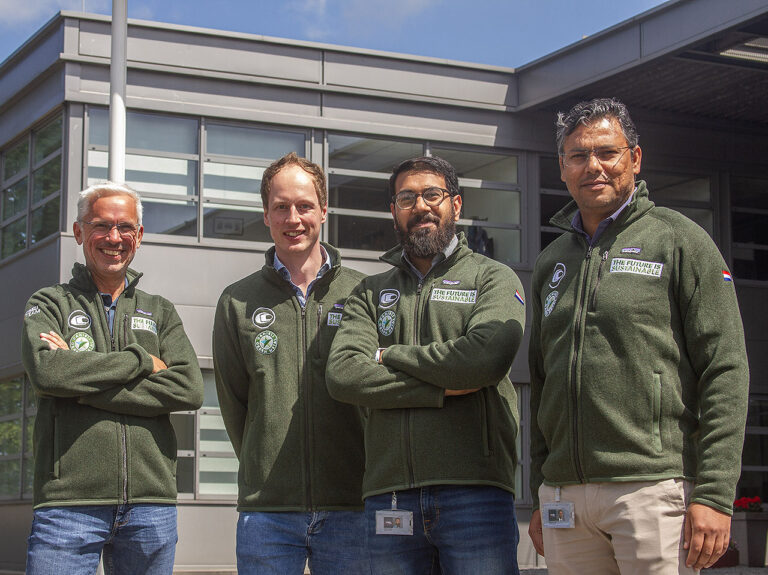
a realistic scenario
The decarbonization of steel production imposes a myriad of challenges. For many steel producers, a realistic scenario that includes BF–BOF steelmaking, is imperative. Our solutions allow for a reduction in BF–BOF steelmaking CO2 emissions of 40%—bringing these emissions in line with those of the traditional DRI–EAF route. Importantly, the scenario allows for financially sustainable implementation by 2030, while being able to produce high–grade steels also when only low–grade ores are available.
Our realistic scenario for BF–BOF steelmaking decarbonization is characterized by low risk and high reward.
“With our realistic scenario, steel industry decarbonization can actually be accelerated”
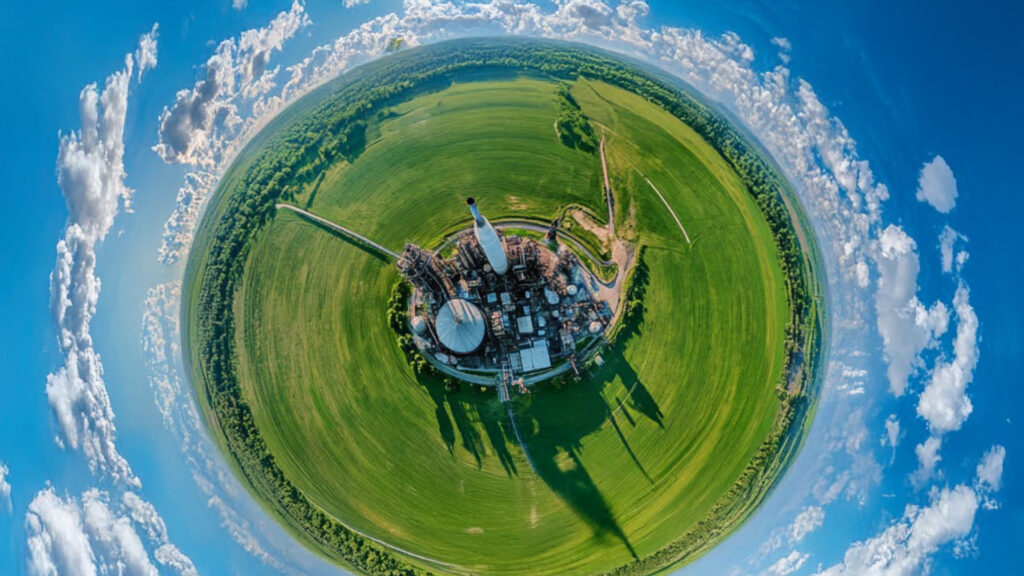
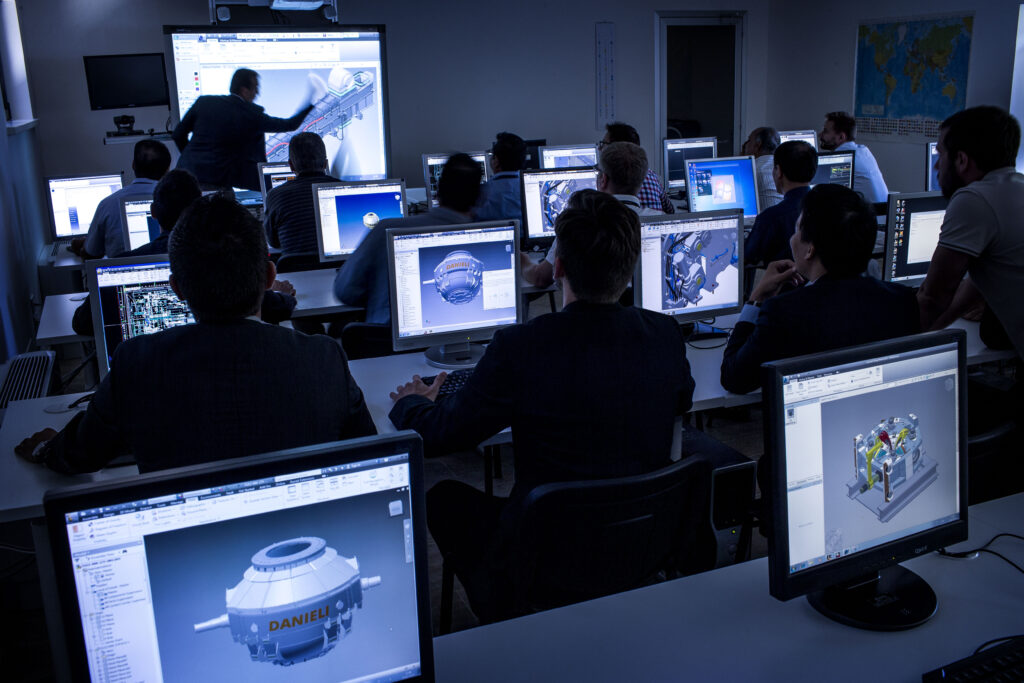
Our People:
our most valued asset
At Danieli Corus, every innovation, breakthrough, and dependable solution is driven by the expertise and resourcefulness of our people. We place our people at the heart of everything we do and we strive to empower them. Their knowledge, creativity and dedication are the true forces behind your progress—and ours.