Upgrades and Improvements in Sublance Sampling and Measurement Technology
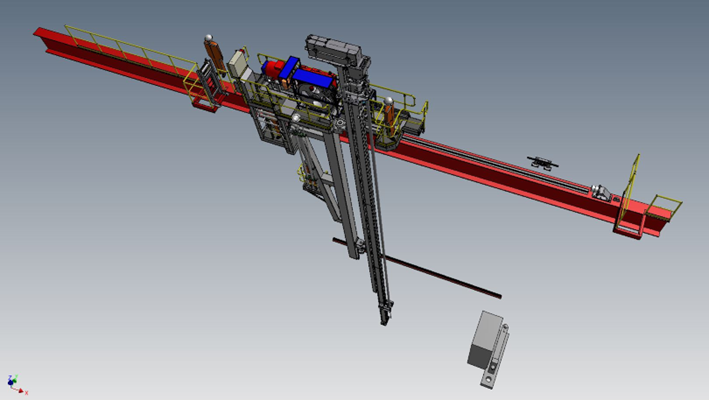
Sublance technology is widely acknowledged as the key BOF process control system. Danieli Corus systems are recognized as the most reliable, with a proven availability of over 98%. All the sublance systems installed by Danieli Corus since 1977 are still in operation, apart from those at BOF shops that were dismantled due to economic reasons. Since the turn of the century, many improvements to equipment as well as process control concepts have been introduced to provide unprecedented levels of automation.
This article, which was presented during the European Oxygen Steelmaking Conference of 2018 in Taranto (Italy) discusses these developments as upgrades that can be implemented for existing sublance systems. The improvement of overall sublance performance is covered, as well as—in some cases—actual inblow temperature measurements and sample taking, which has previously not been possible.
Introduction
Danieli Corus has been active in BOF Steelmaking since 1977, offering primarily Sublance–based BOF Process Control Systems with Level 2 Automation and Hot Metal Desulphurization based on Co–injection of Lime and Magnesium. Danieli entered the converter business in 2011 with the inception of the new, dedicated business unit Danieli Linz. Activities ramped up rapidly in this highly demanding and conservative area of steelmaking. Currently, five BOF converter vessels supplied by Danieli Linz are operating worldwide with sizes between 80 t and 350 t. Another 300 t converter is currently under fabrication.
Since July 2018, the Danieli Corus and Danieli Linz activities have been fully integrated. With this new set–up of integrating the experts of Danieli Linz into the Danieli Corus group, a great opportunity has been launched for further developing equipment in oxygen steelmaking. But on top of that, this is the first time that engineers of an equipment supplier of two disciplines (ironmaking and steelmaking) are working together in a single location. This opens completely new opportunities for the joint development of tools and software for optimizing blast furnace and converter processes in terms of cost and resource savings.
UPGRADES TO EXISTING SUBLANCE SYSTEMS
The Danieli Corus sublances installed in the eighties and nineties are still in operation, apart from those plants being dismantled due to economic reasons. Some of these older sublances are very well maintained by the users, but have never had any mechanical or technical upgrades. As a result of this, as an example, these sublances are lacking a potentially faultless inblow measurement or showing slow slewing movements of the sublance body and carriage guide. Danieli Corus offers these clients a sublance survey that determines the areas of improvement and offers the technical solutions to upgrade the installation to the latest specifications. Several factors determine a successful execution of an inblow measurement under the severe BOF steelmaking blowing conditions. Unsuccessful inblow executions show shortcomings in the following areas including the solutions offered for upgrading:
- User is only capable of doing an intermediate stop or inblow with 10% blowing speed, because sublance uses probes that have a length of 1500 mm. The state of the art Danieli Corus sublance probes have a length of 2000 mm. With this design, the body is protected sufficiently from skull formation by splashing of slag. In case slag is frozen on the body then a good working skull remover on top of the entrance port should be in place.
- For the erevention of bending over a substantial part of the body length resulting in failures during probe connection, revamping the automatic body rotating system or upgrading the guide system can be considered.
- Sublance bodies show severe bending only at the tip end after a few measurements and are changed within a number of heats. The used bodies have a poor design of the internal cooling water circuit. The Danieli Corus designed bodies show long service life that is typically one campaign.
- Inblow measurement lasts too long compared to a new sublance. The remedy is making the sublance faster by improving the PLC control or the speed and position feedback to the PLC. In addition, other critical points are considered like the connection and disconnection of the probe.
Modern computer control is key to fast and accurate signal processing. A next step upgrade for a mechanically improved sublance is done with a DIRC6. The DIRC6 is a measurement computer with enhanced flexibility to future system additions like RFID (Radio Frequency Identification) signal reading. With DIRC6, users have improved system tolerance in carbon and temperature and logging facilities.
REVISED DESIGNS – IMPLEMENTATION IN NARROW SPACES
In the past years Danieli Corus installed more than 130 sublances worldwide in BOF plants with vessel sizes between 100 and 350 tonnes. There is now a tendency for requests for new sublances from BOF plants with space restrictions. The space restrictions come from the corridor between the structural columns and central heart of the vessel or in combination with a small vessel volume. An important figure regarding the space available for the installation of a sublance is the distance between the proposed sublance body position in the vessel mouth and the pivot point close to the column structure. According to our latest sublance design standards, this distance should not be smaller than 1150 mm wide. The minimum allowed distance between main lance and sublance is 200 mm. Recently, Danieli Corus installed three sublances in a Chinese 80 tonnes BOF plant. A combination of a side shifting car for the winch platform with a slewing sublance body system was designed and installed (Figure 1).
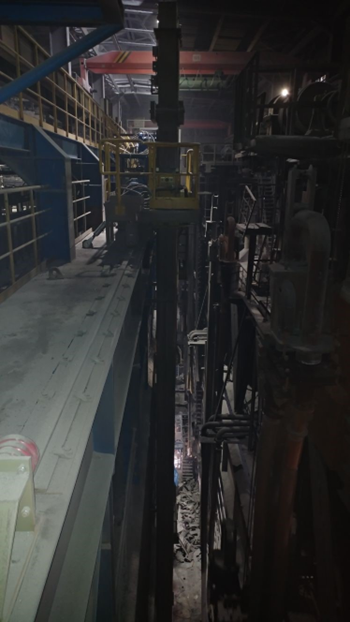
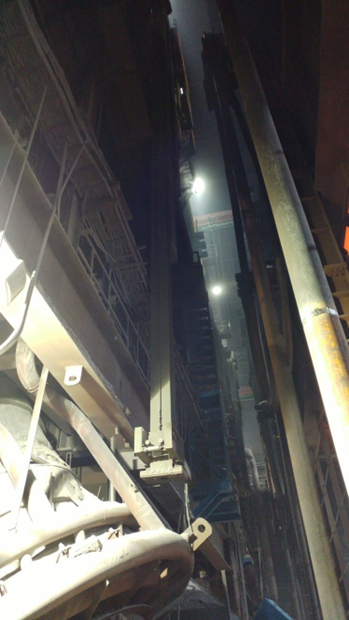
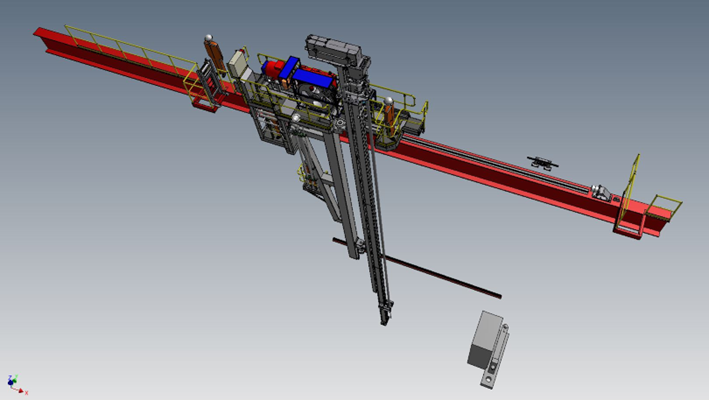
Figure 1 – Side shifting car with slewing sublance body system for 80 T BOF
IMPROVEMENTS TO THE STATIC–DYNAMIC PROCESS MODEL
Controlling the Phosphorus levels during the oxygen blowing process has always been the main driver of the development of the Static–Dynamic model (SDM) of Danieli Corus. During our search for a fast, accurate and reliable tool for Phosphorus prediction, several improvements are launched in the past years like the “Safe Tapping” decision support system in combination with the Danieli Corus TSO–P probe.
Recently, the process model of the support tool has been improved based on trials in a BOF plant resulting in a more accurate prediction of the end Phosphorus in the bath. Even though each system brings an improvement in the Phosphorus control, it also has its limitations. In the end, for the steelmaker it is important to have the correct information to make the right decision regarding the start of tapping process and avoid a penalty afterwards for high Phosphorus. Therefore, the next step in Phosphorus control is based on a technique which relies on a real and fast measurement of the inblow and endblow sublance sample. The technique uses the latest generation of handheld XRF analyzers. These analyzers use a specific technology resulting in accurate and repeatable results in the detection of elements showing weak XRF sensitivity, like Phosphorus and Sulphur.
Combining these XRF analyzers with equipment for fast grinding of metal samples, Danieli Corus succeeded in developing a tool, called FAST (Fast Analyzer Sublance–sample Tool), for fast and accurate analyzes of Phosphorus and other critical elements for the steelmaking process. This product enables the user to measure a Phosphorus concentration down to 50 ppm within 20 seconds and transmit results directly to L2 via Wi–Fi connection.
In case, the user has a sublance system able to disconnect, drop the probe and remove the sample from the probe in 50 sec, then a Phosphorous concentration is available at 70 sec after TSC inblow measurement (Figure 2). In this example, the blowing operator is able to do a correction during the second blow, which takes normally 2 min. A second possibility is to use the endblow sublance sample for FAST. This will lead to a saving in cycle time of about 4 to 5 min and eventually resulting in earlier tapping.
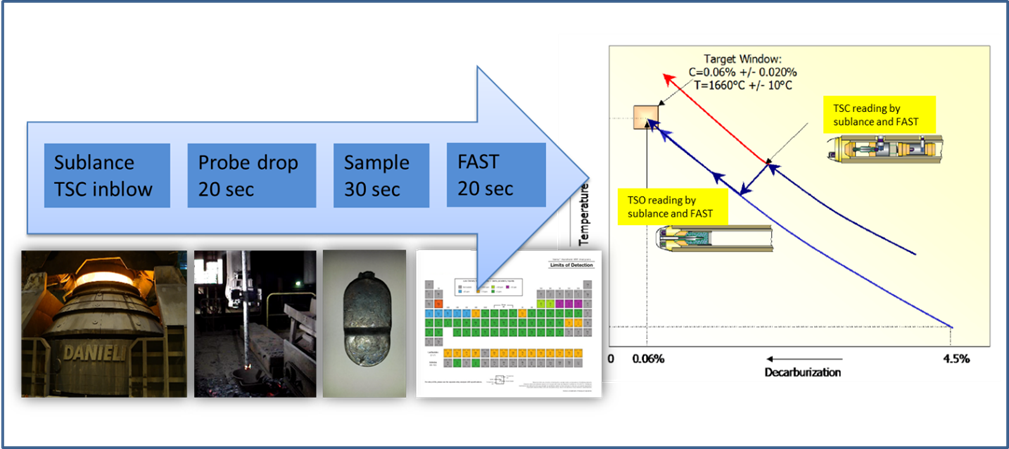
Figure 2 – Typical system timeline for FAST
With the Safe Tapping support system a Phosphorus content in the bath was determined with an error up to 20 ppm. The combination FAST Safe Tapping limits the error down to 8–10 ppm which is an accuracy level comparable to Laboratory analysis.
UPGRADES TO THE HUMAN MACHINE INTERFACE
The SDM communicates via Human Machine Interface (HMI) screens with various operators in the BOF shop, e.g., converter control room, hot metal pit or mixer control room, scrap yard, production coordinator or process control manager, etc. The HMI functions safeguard the following aspects:
- Authority control: restrict each operator to use only the authorized facilities and safeguard that only authorized users can change or update certain data
- User–friendliness: use an overall menu–structure which is clear and easy to handle
- Primary input check: check each input data directly and warn or restrict in case of exceeding ‘plausible’ boundaries
- Status control: check whether any activated function is in compliance with the actual status of the involved heat to ensure a reliable operation.
- The latest generation HMI’s are equipped with remote access to allow assigned computers to have access into the HMI via a web–based interface.
CONCLUSIONS
Sublance–based BOF Process Control has become common practice in the global steel industry over the past four decades. Although early measurement systems were mechanically robust and have proven to be able to operate without problems in the harsh operating environment above the converter hood, these systems lack the latest developments in terms of both hardware and software.
The majority of the modernization of the system has taken place since around 2000, in line with the availability of new technology facilitating these developments. Many of the benefits of systems developed during recent years are available for the end–users of earlier systems since they can be implemented as retrofits.
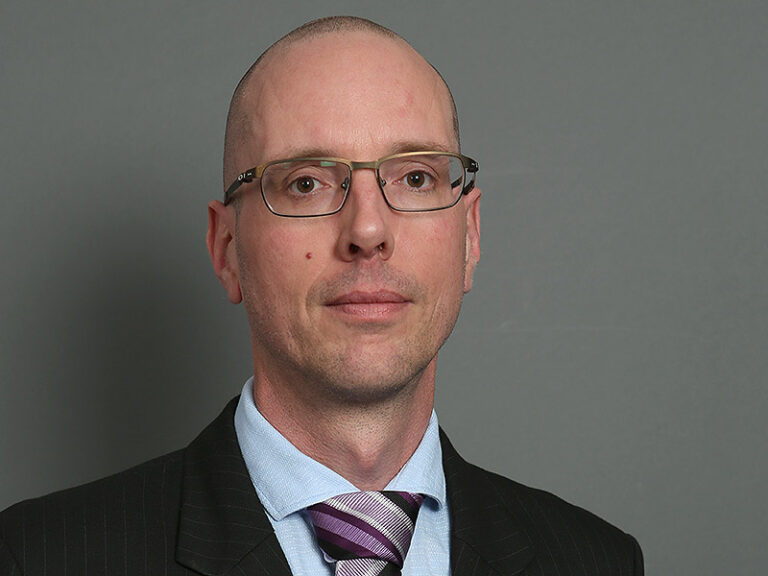
"*" indicates required fields