Blast Furnace Staves Replacement using Fishing Methodology
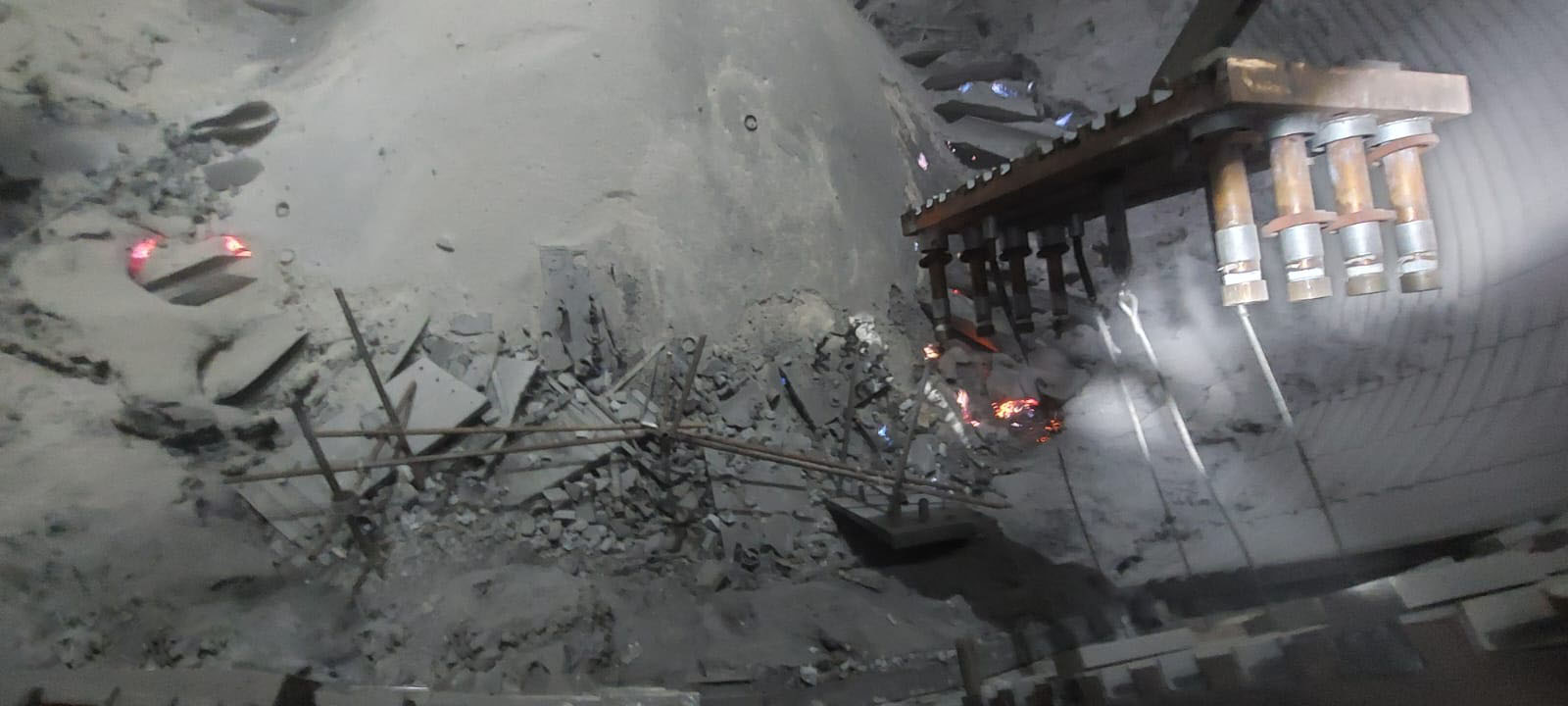
Background
In a large integrated steel plant, the blast furnace cooling system relies heavily on cooling staves (either copper or cast iron) to protect the furnace shell from extreme temperatures.
Over time, these staves can crack or erode due to thermal cycling, abrasion, and chemical attack. In this case, a mid-campaign inspection revealed severe damage to several staves in the Bosh zone. Immediate replacement was necessary to prevent further degradation and potential furnace shutdown.
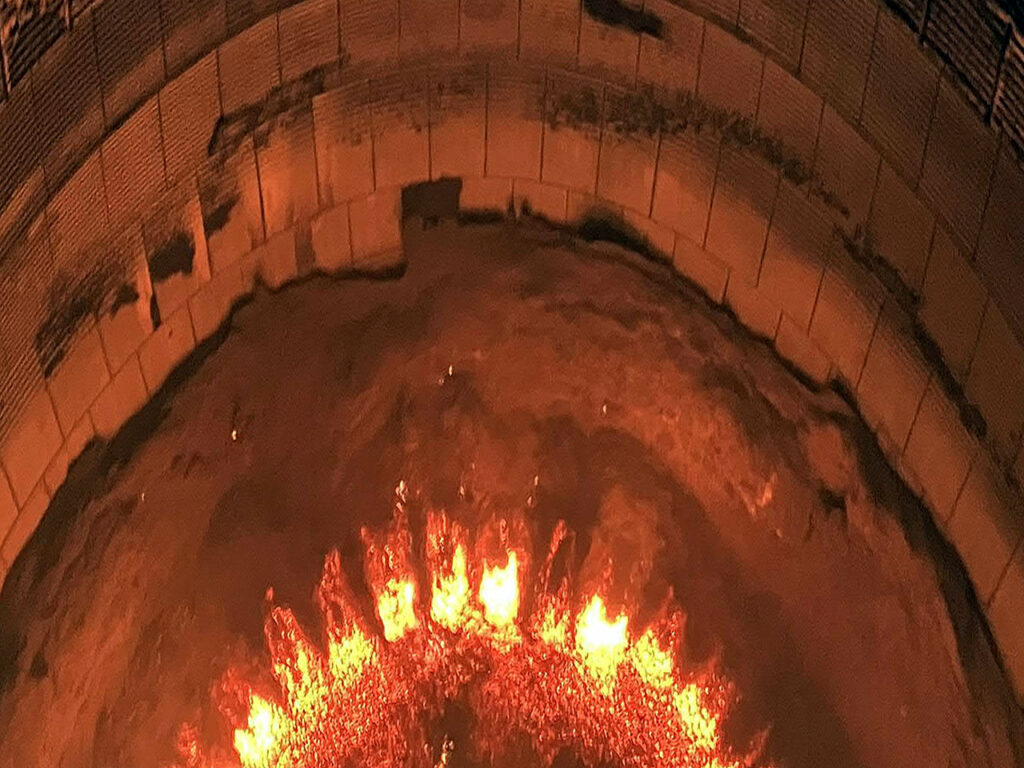
Challenge
Traditional stave replacement methods require manpower within the furnace, introducing safety hazards of which the mitigation measures (such as burden capping, removal of scabs and closing of downcomers) can be time–consuming. Even though these measures are available and feasible, it is always preferred to keep people away from hazards.
Due to the limited time available and project–specific conditions, it was therefore decided to perform stave replacement without any manpower entering the furnace.
The furnace still needs to be blown down, the burden needs to be capped very carefully and safety risks related to potential CO emissions emanating from inside the vessel are not eliminated.
Solution: “Fishing” Method
The maintenance team opted for the fishing method, a specialized technique that allows for the removal and replacement of staves from the furnace exterior.
This method involves:
- Pushing the damaged staves into the furnace in controlled manner
- (Partial) Installation of new blast furnace shell sections
- Drilling access holes through the furnace shell at the stave location
- Inserting a custom designed lifting tool on the Top Charging Unit.
- Inserting custom–designed hooks or “fishing tools” to latch onto the new stave.
- Inserting a new stave, pre–fitted with cooling pipes and sealing materials, using guide rails and hydraulic assistance
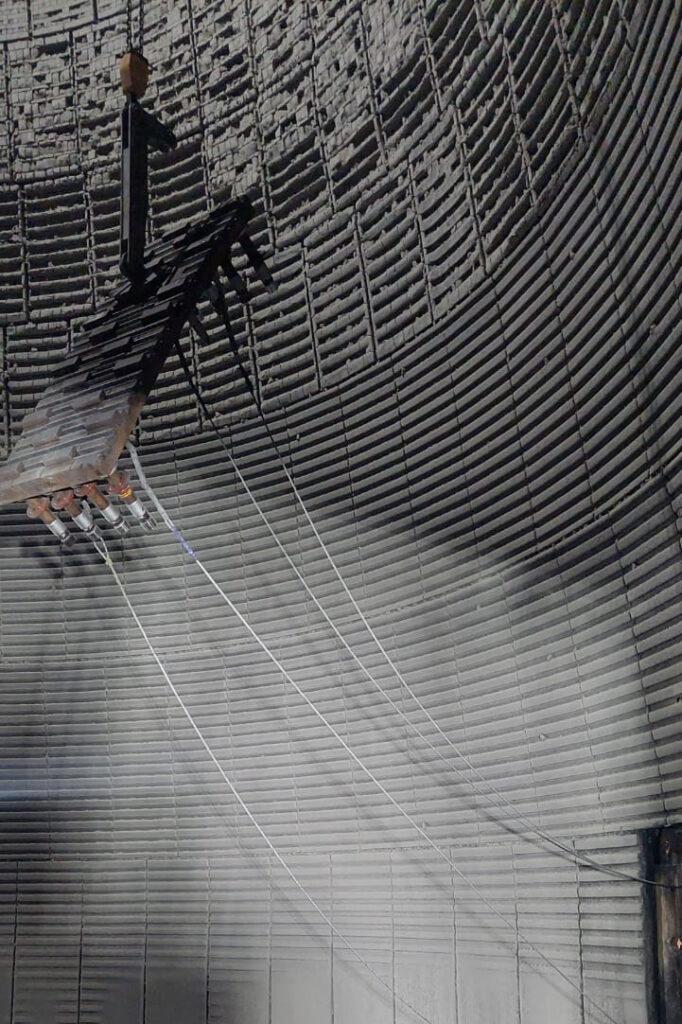
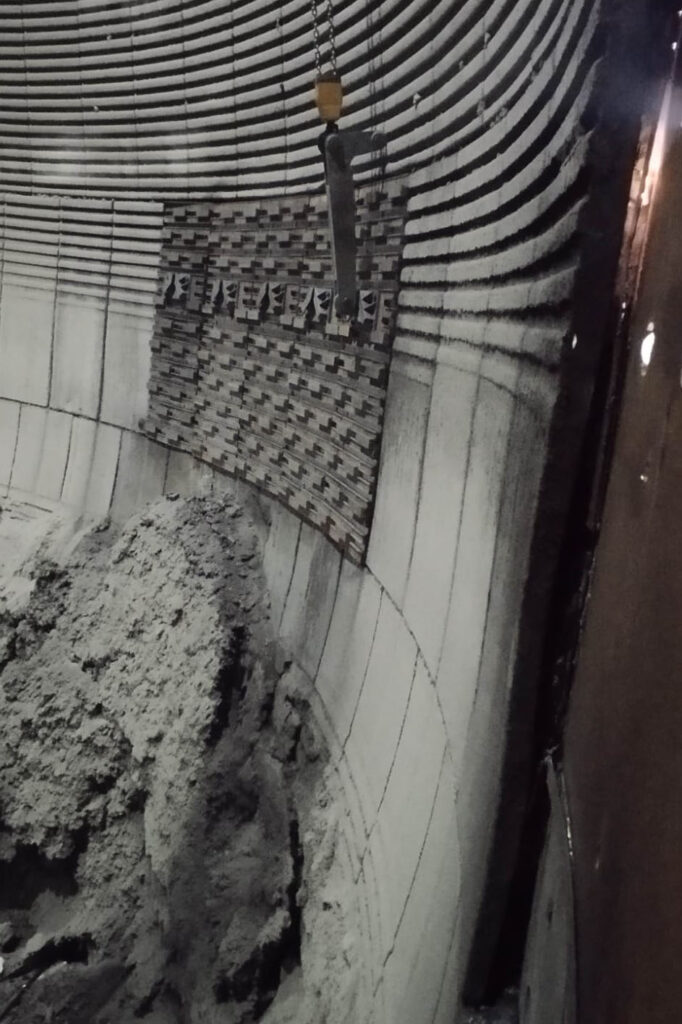
Execution
The operation was carried out over a 10–day period. A total of seventeen staves were replaced using this method. Real-time thermal imaging and shell temperature monitoring ensured that the furnace integrity was maintained throughout the process. The team worked in shifts to minimize exposure and ensure continuous progress.
Results
- Zero Lost Time Incidents were recorded.
- The integrity of the furnace shell was preserved.
- The new staves were successfully integrated into the existing cooling system.
- The fishing method reduced the replacement time by 40% compared to conventional methods.
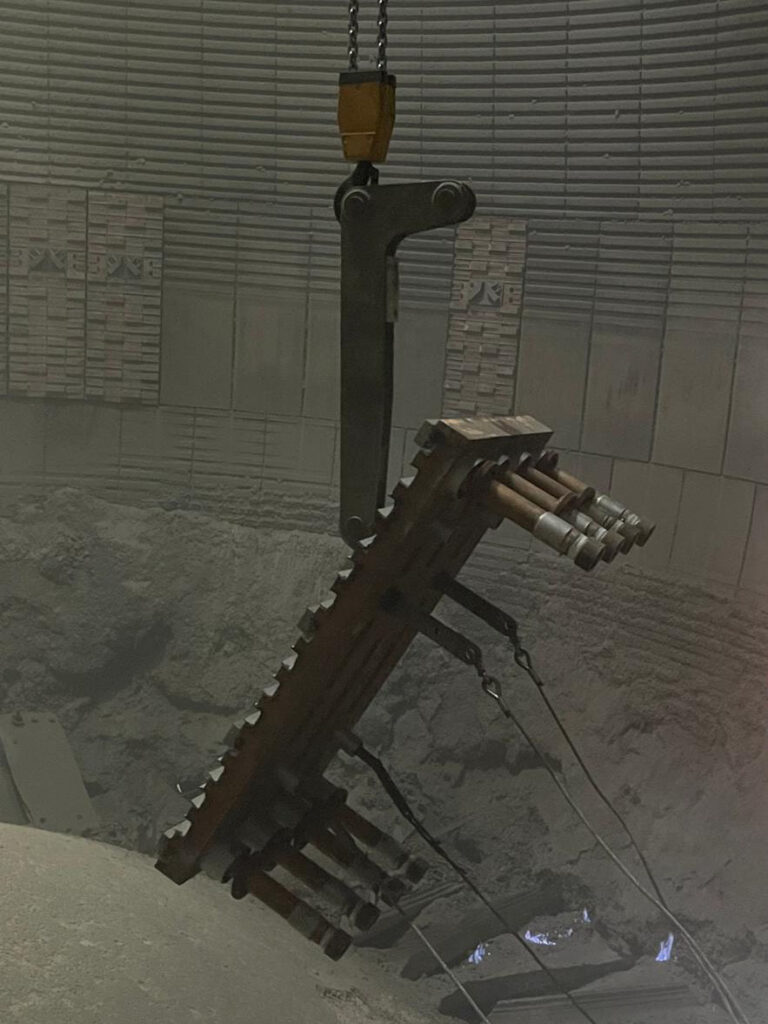
Conclusion
The fishing method proved to be a highly effective and innovative solution for in–situ stave replacement. It minimized operational disruption, enhanced safety, and extended the campaign life of the blast furnace. This case highlights the importance of adaptive maintenance strategies in high-temperature industrial environments
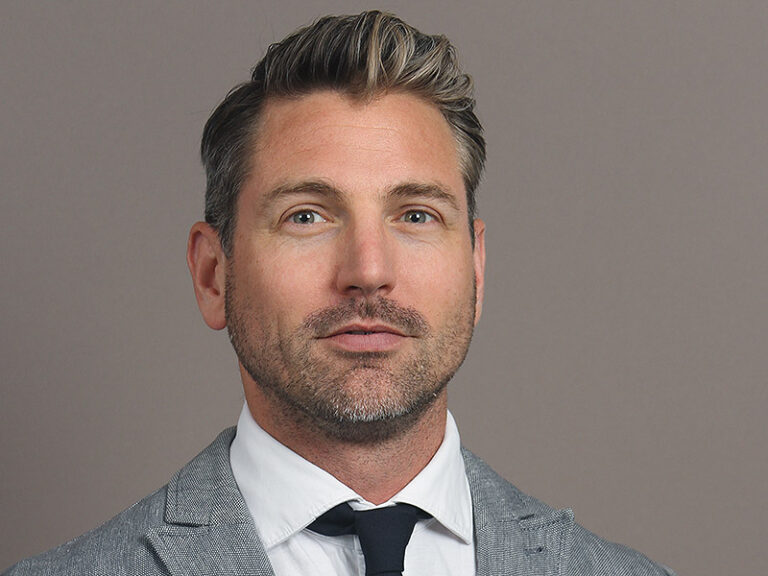
"*" indicates required fields