BF–BOF Steelmaking CO2 Emissions Reduction Options
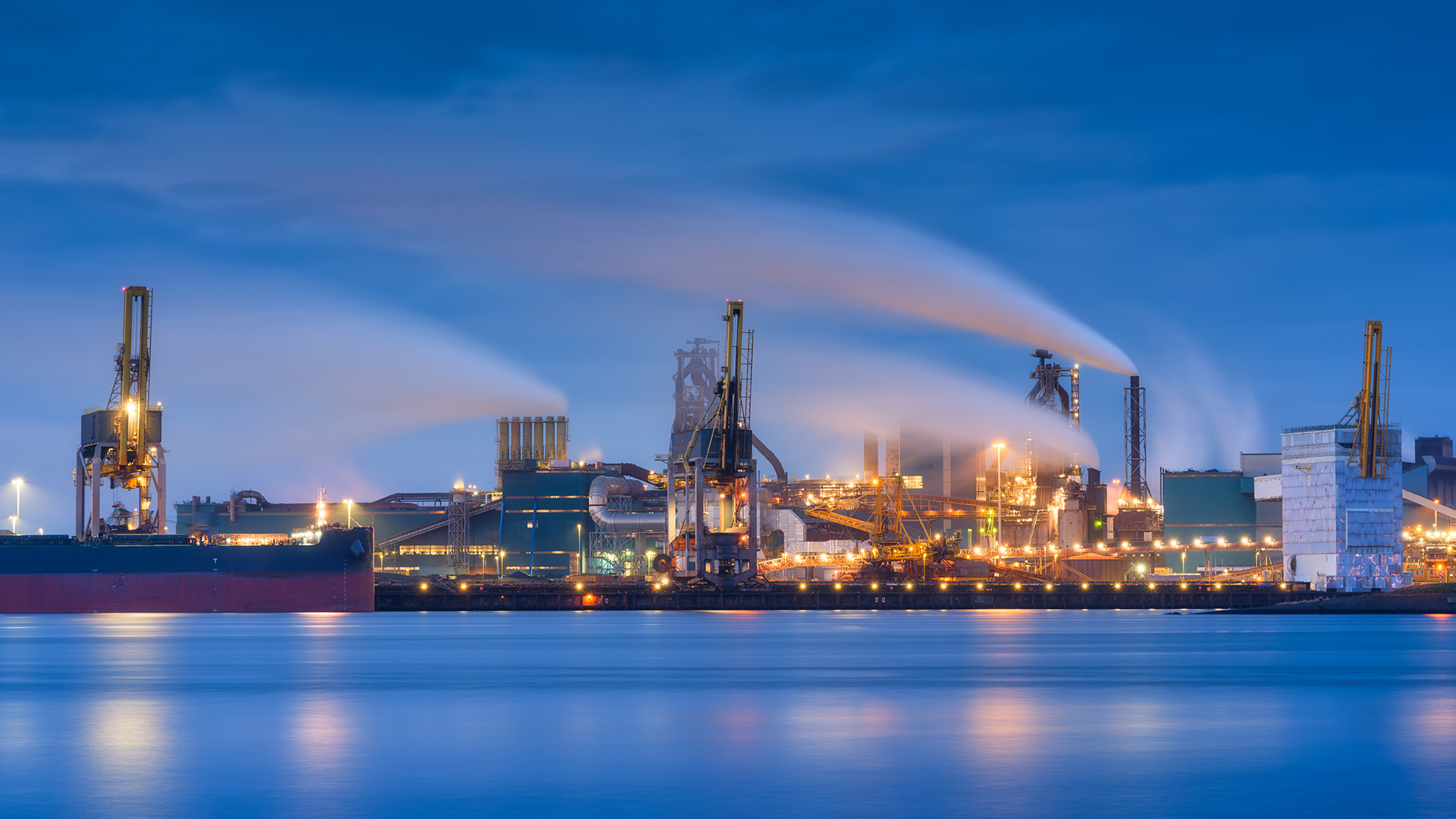
Typical BF-BOF steelmaking CO₂ emissions currently amount to more than 2.0 tCO₂/tCS. Emissions for (DRP–)EAF steelmaking are significantly lower, but this route requires large amounts of NG, H2, electricity and high-grade ores. The efficiency, yield, capacity, quality and economics of modern BF–BOF steelmaking is undisputed, but it will be necessary to significantly reduce the CO₂ emissions to sustain this route. This article, which was presented during the European Coke and Ironmaking Conference in Bardolino in 2024, addresses CO₂ emissions reduction options which could be implemented in BF–BOF steelmaking to reduce the CO₂ emissions significantly.
Introduction
The iron- and steelmaking industry is exposed to significant challenges and risks to reduce the CO2 emissions as these currently account for ~7% of all anthropogenic emissions. Examples of these challenges and risks include an uncertain customer demand for “green steel” and the associated price premiums, availability and prices of raw materials and fuel (e.g. scrap, high-grade iron ores, green electricity & hydrogen), certification, investments, supply chain securities and depreciation of modern assets.
The majority of steel is currently being made by BF–BOF due to its efficiency, yield, capacity, capability to process low-grade ores and produce high-grade steel and its competitive economics. Our corporate forecasts suggest that BF-BOF steelmaking capacity will also exceed one billion tonnes per year in the coming decades despite political, legal and economical net-zero frameworks which are set-up for example in Europe.
Typical BF–BOF steelmaking CO2 emissions in our industry currently amount to more than 2.0 tCO2/tCS. Other mature ironmaking and steelmaking technologies – including DRP and EAF – generate much lower CO2 emissions particularly if green electricity and hydrogen would be used, but introduce specific challenges and risks as mentioned afore.
Our company is therefore determined to aid the steelmaking industry to significantly reduce BF–BOF CO2 emissions along two timelines i.e. Phase 1 (short-term) and Phase 2 (mid-term) improvements. In Phase 1 BF-BOF CO2 emissions could be reduced to ~1.7 tCO2/tCS by optimum selection of raw materials, optimization of operations and logistics and implementation of mature plant engineering technologies. Meanwhile, we are advancing our development program to reduce the CO2 emissions to ~1.2 tCO2/tCS using alternative BF ironmaking and BOF steelmaking technologies which could be deployed in Phase 2 after successful industrial demonstration.
This paper summarizes our proposals and recommendations for short and mid term improvements to reduce BF–BOF CO2 emissions and secure competitive operations and economics in order to allow the steelmaking industry more time to decide upon more fundamental changes to iron- and steelmaking technologies using other technologies such as DRP and EAF.
BF-BOF CO2 Emissions
The authors have set-up spreadsheet and flowsheet models to calculate and estimate BF–BOF CO2 emissions. The results of our calculations have been compared to industrial plant data from our clients and the calculations are sufficiently accurate to estimate the effect of CO2 emissions reduction improvements. Our calculations and estimates include Scope 1 emissions generated by sintermaking, cokemaking, pelletmaking, (BF and DRP) ironmaking, steelmaking and casting.
It is assumed that sufficient process gases are generated to produce electricity for the entire plant (including other upstream and downstream facilities e.g. raw material handling system, cold strip mill and finishing line). Consequentially Scope 2 emissions are effectively set to zero. It is also assumed that electricity generation suffices for the production of steam, oxygen, nitrogen and argon. Carbon inputs include mainly coke, coal, fluxes, NG and a limited amount is also included in scrap/HBI/DRI.
Scope 1 emissions for sintermaking, pelletmaking, cokemaking and casting are calculated by using specific CO2 emissions for each of these facilities and are listed in Table 1. These specific emissions will actually be different for each site and also depend on specific process technologies.
Table 1 – Specific CO2 emissions
Plant Area | CO2 | Unit |
Sintermaking | 250 | kg CO2/tSinter |
Pelletmaking | 150 | kg CO2/tPellets |
Cokemaking | 300 | kg CO2/tCoke |
Casting | 50 | kg CO2/tCS |
Specific CO2 emissions for ironmaking and steelmaking have been determined by using steady-state mass and energy balances and also account for yield losses.
An example of our CO2 emission calculations is summarized in Table 2 assuming coke and PCI rates of 320 kg/tHM and 180 kg/tHM in BF ironmaking and 15% scrap rate in BOF steelmaking. This example reflects modern and efficient iron- and steelmaking and is considered the base case.
Table 2 – CO2 Emissions Base Case
CO2 Emissions kg CO2/tCS | ||
Sintermaking | 270 | kg CO2/tCS |
Pelletmaking | 68 | kg CO2/tCS |
Cokemaking | 93 | kg CO2/tCS |
Ironmaking | 1334 | kg CO2/tCS |
Steelmaking | 192 | kg CO2/tCS |
Casting | 51 | kg CO2/tCS |
Grand Total | 2007 | kg CO2/tCS |
Short- and mid-term improvements – i.e., reductions of CO2 emissions – will be discussed in the next sections.
Phase 1: Short–term CO2 Emissions Reduction Options
The authors are proposing short–term improvements to ironmaking and steelmaking to reduce the CO2 emissions to ~1.7 tCO2/tCS. These improvements mainly include changes to raw materials, improvements of energy efficiency, logistics and operations without necessary capital investments. Examples will be discussed in the sub-sections hereunder.
Blast Furnace Ironmaking
Reductions of BF ironmaking CO2 emissions can be accomplished by reductions of the coke and coal injection rates. Examples include – but are not limited to:
- Maximize metallics in the burden
- Maximize pellets and minimize sinter in the burden
- Minimize slag volume e.g. minimize Al2O3 and SiO2 in pellets and sinter
- Replace PCI with less CO2 intense fuel (NG/COG/H2 injection)
- Minimize ash content of coke and coal
- Minimize burden moisture, (raw) fluxes, steam injection
- Maximize gas utilization, oxygen enrichment
- Maximize yield, fines/reverts recycling
- Maximize hot blast temperature e.g. by using energy-saving tuyere stocks and tuyeres
Basic Oxygen Furnace Steelmaking
Reductions of BF–BOF CO2 emissions can be accomplished by using minimum hot metal and maximizing scrap/HBI/DRI in BOF steelmaking. Examples of methods to maximize scrap/HBI/DRI and other options to improve BOF steelmaking include:
- Optimize logistics to ensure maximum hot metal temperatures
- Minimize (raw) fluxes
- Minimize converter tapping temperature
- Minimize yield losses
- Scrap preheating
- Maximize energy efficiency e.g. utilization of BOFG, usage of ladle covers, etc.
The total CO2 emissions can be reduced to ~1.7 tCO2/tCS if these changes are implemented as summarized in Table 3.
Table 3 – CO2 Emissions including short-term improvements
CO2 Emissions kg CO2/tCS | ||
Sintermaking | 22 | kg CO2/tCS |
Pelletmaking | 138 | kg CO2/tCS |
Cokemaking | 85 | kg CO2/tCS |
Ironmaking | 1140 | kg CO2/tCS |
Steelmaking | 270 | kg CO2/tCS |
Casting | 51 | kg CO2/tCS |
Grand Total | 1706 | kg CO2/tCS |
Phase 2: Mid–term CO2 Emissions Reduction Options
More significant CO2 emissions reduction requires more fundamental changes to BF ironmaking and BOF steelmaking and stretching of conventional contemporary process and operations limits. These changes will require plant engineering and logistics modifications, capital investments and will also impact operations. The authors propose different BF and BOF technologies and options for a more significant reduction of BF–BOF CO2 emissions. Gas conditioning technologies are also addressed as it may be necessary to capture BFG and BOFG CO2 before either sequestration or conversion to other products.
Blast Furnace Ironmaking
The contribution of BF ironmaking to the CO2 emissions could be more significantly reduced if the amount of metallics in the burden is increased to ≥ 300 kg/tHM, the coke rate is reduced to ~250 kg/tHM and NG+H2 injection is increased to > 120 kg/tHM. Thermal limits (RAFT, top gas temperature) will be exceeded unless auxiliary heat is transferred to the process. This could be accomplished by different options using e.g. shaft injection and electrical heaters. Our electrical heater assessments are suggesting favorable economics if factoring in the costs of CO2 emissions, but will require “green” electricity as otherwise CO2 emissions will be shifted from scope 1 to scope 2. Industrial demonstration of shaft injection and electrical heater technologies are necessary to determine and confirm their efficiencies and availabilities.
Basic Oxygen Furnace Steelmaking
Minimizing BF hot metal in BOF steelmaking will also have a significant impact on reducing BFiBOF CO2 emissions. This can be accomplished by maximizing scrap, HBI and DRI in the BOF charge mix, ideally beyond 40%. Additional heat must be transferred to BOF steelmaking as otherwise thermal limits will be exceeded. This heat could be either generated by using high-carbon DRI, injection of carbon and/or (electrical or gas) pre-heating of the metallics. We are currently assuming that both options will be necessary.
Another advantage of decreasing hot metal in BOF steelmaking to < 60% relates to the fact that one BF may be shut-down if three – or more – BF’s are currently operating to produce > 80% hot metal for BOF steelmaking assuming that the BF productivity could be reasonably increased.
The total CO2 emissions can be reduced to ~1.2 tCO2/tCS if these changes are implemented as summarized in Table 4.
Table 4 – CO2 Emissions including mid-term improvements
CO2 Emissions kgCO2/tCS | ||
Sintermaking | 0 | kg CO2/tCS |
Pelletmaking | 102 | kg CO2/tCS |
Cokemaking | 48 | kg CO2/tCS |
Ironmaking | 707 | kg CO2/tCS |
Steelmaking | 300 | kg CO2/tCS |
Casting | 51 | kg CO2/tCS |
Grand Total | 1208 | kg CO2/tCS |
Gas Conditioning
Ultimately it may become necessary to deploy gas conditioning technologies to capture CO2 and convert it to other products. This could hypothetically reduce BF–BOF CO2 emissions to much lower levels than ~1.2 tCO2/tCS if sustainable energy, electricity and H2 would be used. However, the economics are yet unclear and may favor conversion to other iron- and steelmaking technologies instead.
We are currently evaluating the feasibility of different CO2 capturing technologies including:
- Chemical absorption
- Physical absorption and adsorption
- Membrane gas separation
- Chemical looping
CO2 sequestration may be a temporary method to reduce CO2 emissions to the atmosphere to limit (anthropogenic) climate change, but large reservoirs are not readily available in many regions. Instead mineralization of CO2 may be more realistic and is therefore also pursued in our industry.
It is also proposed to consider alternative utilization technologies to convert CO2 to other products. Stochiometric reforming and reverse water gas shift reactors are potential options of interest.
Energy balances, economics, space requirements, etc. will be decisive to conclude the feasibility of any gas conditioning technologies within the iron- and steelmaking industry.
Conclusions
The authors expect that BF–BOF steelmaking will be retained in our industry for the coming decades, representing annual global capacities of more than one billion tonnes. The reason for this is that this route has specific advantages to alternative ironmaking and steelmaking technologies. Meanwhile, contemporary and common opinion requests CO2 emissions reduction to limit (anthropogenic) climate change.
It is concluded that short-term and mid–term CO2 emissions reduction is possible to more than 15% and 40%, respectively.
Short-term CO2 emissions reduction options mainly include changes to BF burden and BOF charge mix materials i.e. maximum usage of scrap/HBI/DRI and maximum usage of gas instead of coal. These short-term options can be deployed without significant changes to plant engineering and without capital investments.
Mid-term CO2 emissions reduction options will require more significant changes to BF–BOF ironmaking and steelmaking and implementation of new technologies in order to further increase usage of scrap/HBI/DRI, increase energy efficiency and less CO2 intense fuel. Industrial demonstration of these technologies is mandatory to confirm their efficiency and availability.
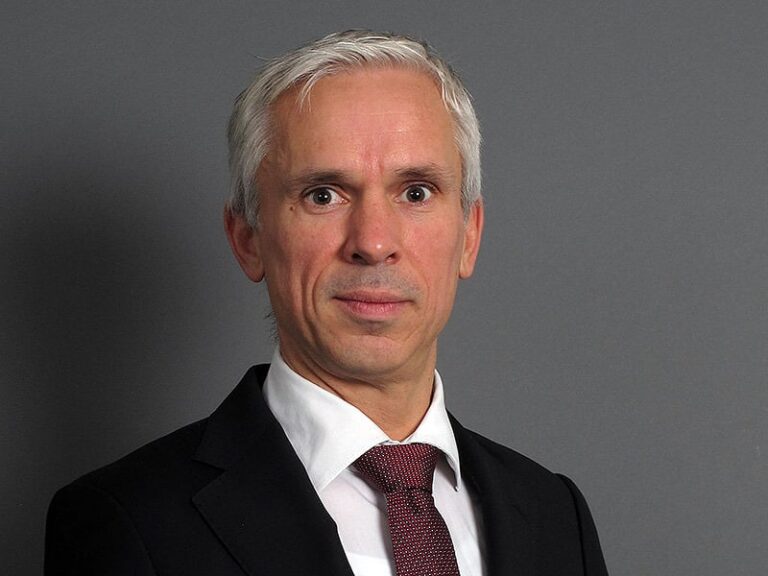
"*" indicates required fields