A Robust FTC for the Global Aluminium Industry
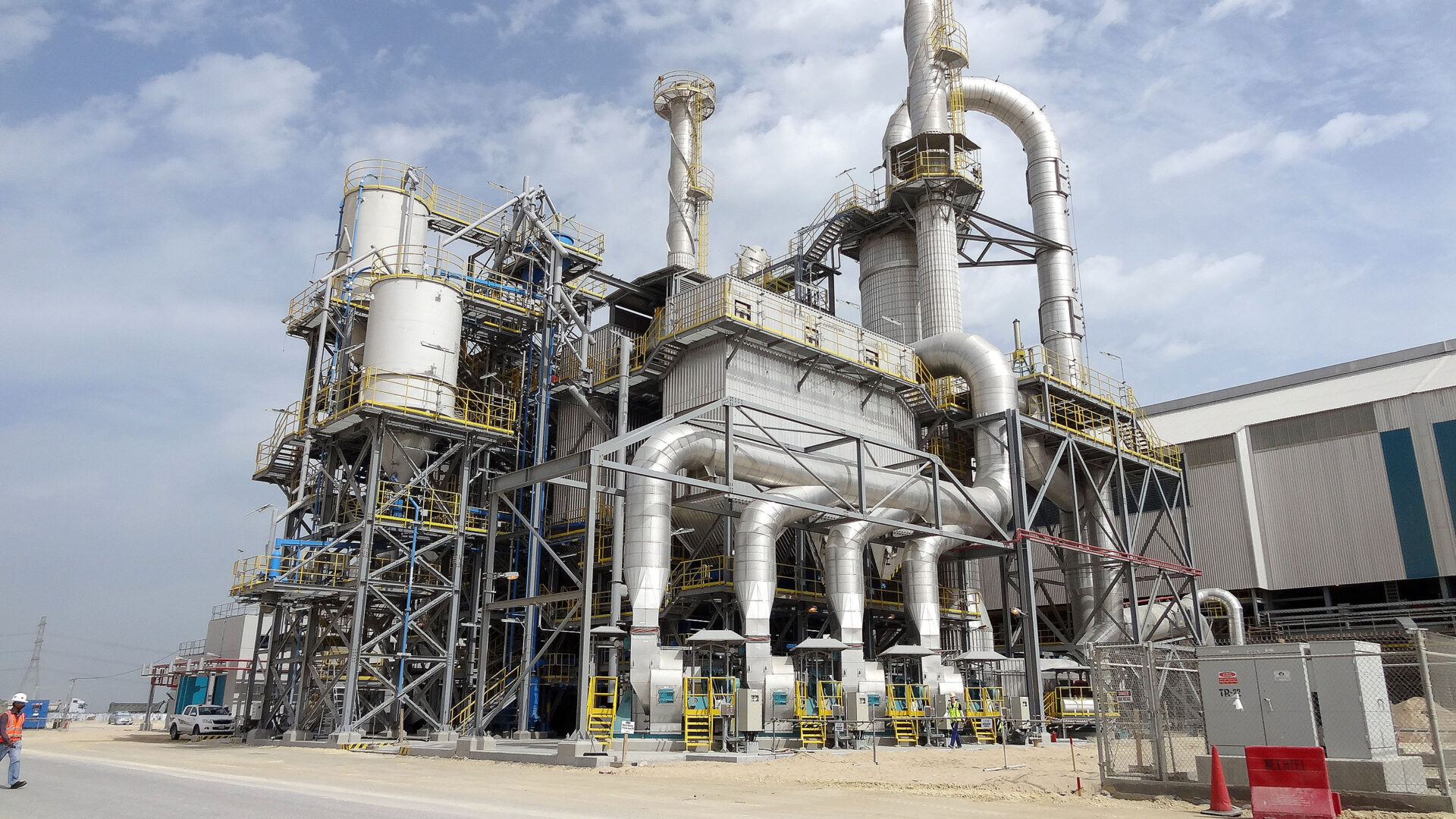
Who does not remember the Toyota Landcruiser that the team of Top Gear mistreated in their show? Despite all the abuse, each time the Toyota was brought back to life with a few simple tools. The Fume Treatment Centre of Danieli Corus has many similarities; it does not matter what you do to it; it will perform. The original Pleno design was developed by a former maintenance manager at a primary aluminium smelter in the eighties. At that time, this maintenance manager was not pleased with the equipment given to him, so he decided to manufacture his own gas cleaning equipment. Currently the fifth generation of the Pleno Design is on the market. Experience shows that hot temperatures, sparks, tar, dust will all be handled. Also, poor operation or lack of maintenance has little effect on the operation of the FTC. In the paper we will show examples of the performance of the FTC during extreme conditions and how any damage could be repaired easily. This article was presented at the ICSOBA 2024 conference in Lyon, France.
Introduction: Pleno V Fume Treatment Centers
The Fume Treatment Centre designed by Danieli Corus for the primary aluminium smelting sector has shown its robustness and reliability over decades. Now in its fifth generation the Pleno design has been updated and improved while retaining its tried and tested design. Pleno V relies on a design dating back to the 1980s that has proved itself over the years, while undergoing improvements in each successive generation. The Pleno V design as seen in figure 1, provides additional platforms, easy access for inspection and maintenance, and isolation points.
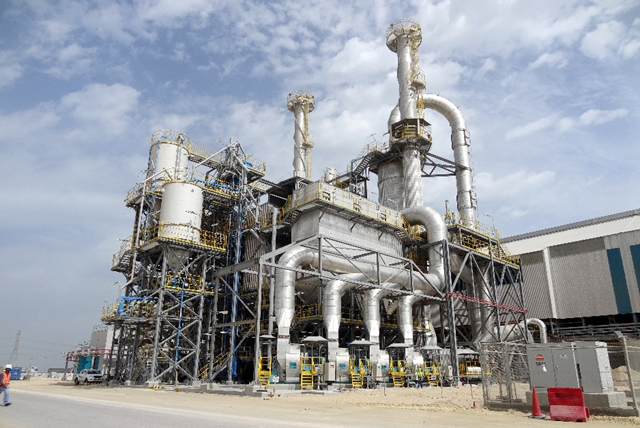
Figure 1 – Pleno V Fume Treatment Center
A key component of the FTC is the conditioning tower, a component that must be strong, robust and built to withstand corrosive atmospheres and high temperatures. Conditioning tower design, operation and replacement were discussed in previous publications [1,2,3].
The Conditioning Tower
The conditioning tower’s main purpose is to condense and remove volatile pollutants, Polyaromatic Hydrocarbons (PAH) and particulates. A constant temperature of approximately (105-110) °C at the outlet of the conditioning tower, but not above is key.
The robust conditioning tower conservatively designed by Danieli Corus, has been known worldwide as a reliable means of cooling the bake furnace fume for the past 25-30 years. To facilitate the complete evaporation of the water droplets inside the cooling tower, a special atomizing nozzle has been selected which uses water and compressed air to create a very fine mist of water droplets in the gas flow. This fine mist allows complete evaporation of the water in just a few seconds, well before the mist reaches the bottom of the tower. The cooling tower has been designed conservatively, using a residence time of 8 seconds at the design conditions, ensuring complete evaporation while sustaining a fume outlet temperature of 105 °C. This generous evaporation time in combination with the flexibility to use up to 7 spray nozzles will continue normal operation when a single lance is removed for maintenance. The Hastelloy spray nozzle and stainless-steel lance body is equipped with quick-disconnect coupling for easy maintenance. A set of 3 inlet- and outlet temperature sensors on the conditioning tower will monitor the process. A false reading is automatically discarded by the control system to prevent unwanted bypass operation.
The conditioning tower cools flue gases to a constant temperature, irrespective of varying heat load, gas throughput, changes in raw material supply and disrupted operating conditions. It targets > 99.5 % online availability which equates to less than 48 hours downtime per year.
“Dry Bottom” Operation
“Dry bottom” operation of the conditioning tower as seen in figure 2, is the operating mode whereby pollutants are discharged at the bottom without containing any moisture. This reduces corrosion risk and makes for a service life of 30 years and more, against typical design life of 20 years.
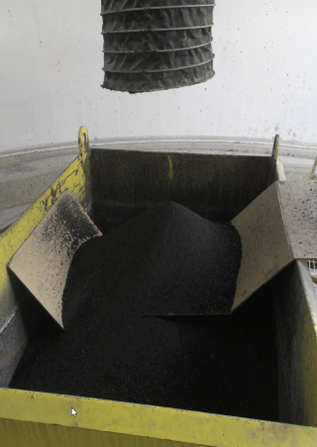
Figure 2 – Separated pollutants with “dry bottom” operation
The Sulphur content in the petroleum coke has increased over the years following restrictions on Sulphur in fuels such as diesel, leaving more Sulphur in the coke. This has led to a rise in Sulphur dioxide (SO2) and, along with increased concentration of vanadium (V) in the petroleum coke, a rise in Sulphur trioxide (SO3) in the flue gases. The presence of moisture results in highly corrosive sulphuric acid (H2SO4). So, the improved environmental standards for liquid fossil fuels are generating a serious corrosion problem through chemical attack on the FTC equipment. This makes a dry bottom essential for long service life in the conditioning tower.
Automated Temperature Control
Highly automated temperature control, with three sensors on the inlet and three on the outlet ensure constant temperature, allow total evaporation of the water spray and prevent condensation, ensuring a straight temperature line throughout the process – refer to figure 3. Feed forward control on the quantity of gas passing through provides information in advance to the control system to support this control.
In the feed forward control, the incoming heat load is calculated by multiplying the gas volume, measured at the stack, by the temperature measured by the inlet of the riser duct. As the desired outlet temperature is known, it is possible to calculate the amount of water required. This value is given as start point for the water control valve. The final adjustment of the water control valve is done by the outlet temperature of the conditioning tower. Large swings in flow or temperature are therefore detected early and can be handled without any problem. The setpoint for the conditioning tower outlet is typically set at 105 °C and will be maintained at +/- 2 °C provided the spray lances are properly maintained. The shape of the conditioning tower, along with the positioning of the spray lances and the coverage they provide make for a high residence/retention time of eight seconds that provides sufficient time for the reactions and the water to evaporate.
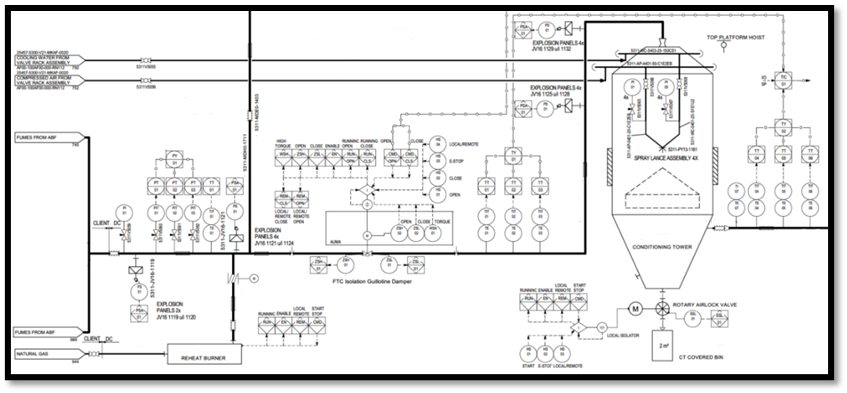
Figure 3 – Control philosophy and instruments of the Conditioning Tower
Robustness
While effective maintenance is essential to extend operating life, experience over decades at our conditioning towers reveals great robustness even in the absence of adequate maintenance. Evidence from conditioning towers installed by us decades ago reveals that even substandard maintenance will not cause the conditioning tower to fail. Examples include failure to clear the spray nozzles and failure to clean alumina handling equipment. The Pleno copes with all these shortcomings and more, including corrosion of the internal diffuser and material accumulation in the inlet plenum. Given effective maintenance, Pleno V has a virtually indefinite operating life.
Accessibility
Another key advantage of the Pleno V is its accessibility for inspection and maintenance, facilitated by full access through platforms and staircases. All systems requiring regular service or maintenance have automatic backups that cut unscheduled downtime and are easily accessible. Hoisting equipment, wide platforms providing storage area, and a good logistic design are provided for easy access and a logic way of working when maintenance is required.
Quality Components
The acid resistant Hastelloy nozzles, along with the conditioning tower coating and regular maintenance, will prevent corrosion of the FTC equipment and ensure a lifespan of over 30 years. The scrubbers are designed to be energy-efficient and easy to maintain during operation.
Despite the conservative design, ease of maintenance and continuous online monitoring, at some facilities the conditioning tower has been subject to severe corrosion to the inner shell, bottom cone and diffuser. The corrosion results from years of malfunctioning water sprays or an upset in the programming. These upsets have gone unaddressed despite several online alarms and visual indications during routine inspections. Danieli Corus has witnessed cases where the shell of the tower has been severely corroded to the point of full replacement and others where the inlet diffuser has to be replaced. Despite these crippling conditions, the Danieli Corus conditioning tower manages to meet the expected performance. The robust design provides ample time to adequately plan and prepare repair procedures.
Conditioning Tower Maintenance
The operational maintenance of the conditioning tower is limited to the inspection of the spray lances. A bi-weekly inspection on the spray pattern of the operational lances is required. All operational lances should be removed and tested one by one. Due to the presence of shut-off ball valves, quick coupling hoses and speedball nuts flanges, the removal of the lances is easy. Once removed, the lance is put on the platform and is reconnected to the hoses and the shut-off valves are opened. The spray pattern should show a plume of mist similar as shown in figure 4A.
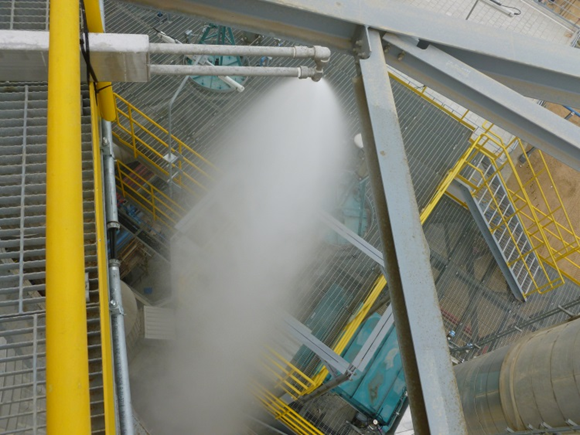
Figure 4A – Inspection of lance spray with correct pattern
Faulty spray patterns demonstrate sideways spraying or dripping as shown in figure 4B. Such patterns are mostly cause by fouled or corroded lances, an example of which is given in figure 4C. Faulty lances should be cleaned or replaced. After the inspection the lance can be re-inserted and put back in operation. In case of mechanical damage of the nozzle, the tip can be exchanged separately.
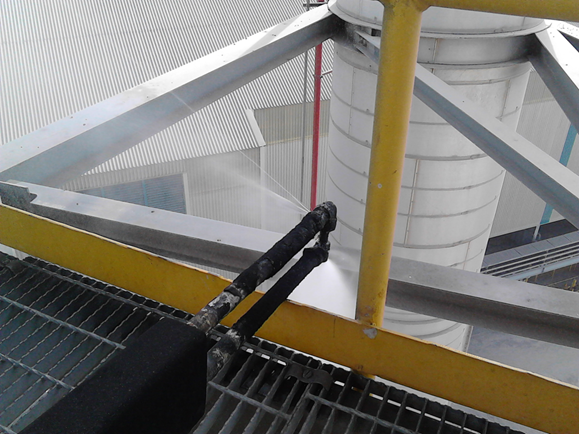
Figure 4B – Inspection of lance spray with faulty pattern
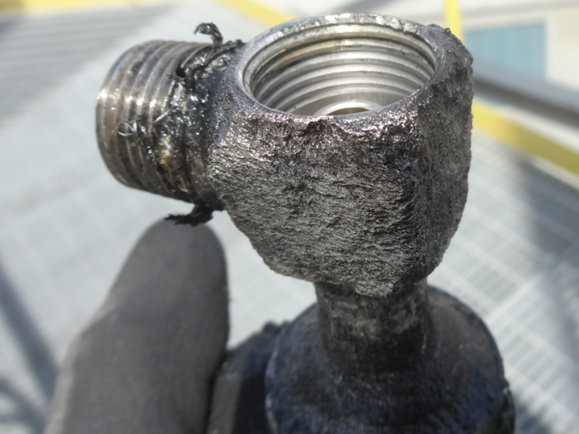
Figure 4C – Fouled spray lance
Wall thickness measurements should be executed once per year. This is advised to monitor and follow any corrosion on the conditioning tower on the inside. If the conditioning tower is operated correctly, no corrosion is expected. The latest generation conditioning tower includes NDT measuring ports at strategic locations on the tower shell. This allows for routine monitoring and checking without disrupting the insulation and lagging. Experience has shown that once the original insulation is compromised, it is rarely repaired and leads to external corrosion of the tower shell. So, the permanent test ports prevent this and provide confidence to the operators of the shell integrity.
During an anode baking furnace stop a visual inspection should be carried out. Manholes near the sprays, in the cylindrical part and in the bottom cone of the conditioning tower allow access and/or inspection possibilities. Any built-up detected should be removed.
Case Study
Our conditioning tower has a reputation of continued performance in extreme operational ranges, spray lance issues and severe corrosion. During a visit to Plant A, inspection of the conditioning tower showed almost complete loss of the internal diffuser, internal duct and the airlock at the bottom of the conditioning tower as per figure 5 on the next page.
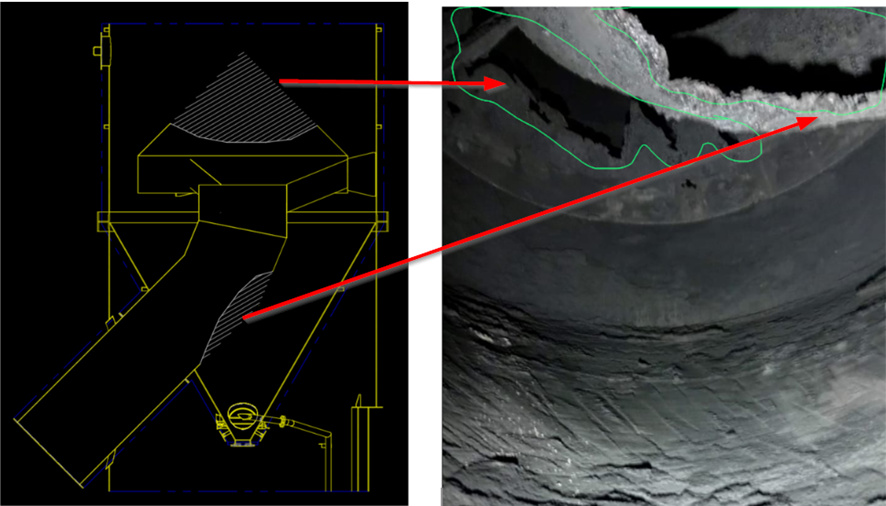
Figure 5 – Corroded diffuser cone and internal duct
With the diffuser out of service, there is potential for hot ambers or large particulate to make its way to the baghouse and cause further damage. This corrosion was direct result of excess spray water caused by compromised spray lances. If the spray nozzle tips are not cleaned, the spray nozzles will suffer corrosion themselves and the injected water is not atomized sufficiently for complete evaporation. Despite the ultra-conservative retention time in the tower, the un-vaporized water droplets collect on the diffuser and cone, ultimately causing corrosion.
This degree of damage does not happen swiftly and there is ample time during routine maintenance and inspection where this could be easily corrected. However, after years of neglect the extent of corrosion is evident, yet the conditioning tower kept performing for many years. The corrosion continued to grow and yet the outlet temperature from the conditioning tower was generally maintained as can be seen in figure 6: this screenshot shows the inlet and outlet temperatures of the conditioning tower over time and clearly demonstrates that despite major swings in inlet temperature (which is inherent to the nature of the ABF), outlet temperatures remain very stable.
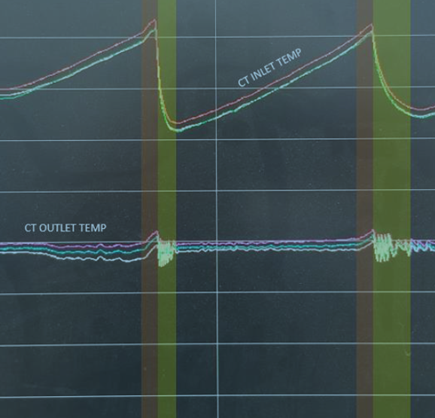
Figure 6 – Conditioning tower inlet and outlet temperatures observed during fact finding
The robustness of our conditioning tower is evident. Obviously, the goal of the installation is to maintain and prolong the life of the conditioning tower indefinitely, but circumstances arise where this is not the case. It is comfortable knowing that when proper maintenance and inspection is not sustained that catastrophic failure is not immediate.
We are currently managing a project at Plant A aimed at remediating the conditioning tower. This initiative involves establishing a comprehensive repair strategy, overseeing both the design phase and on-site execution.
The design involves creating an additional supporting system to enable the partial removal of the conditioning tower’s supporting skirt. This skirt needed to be cut to allow the installation of three fully assembled parts, minimizing downtime. The second part of the design includes an engineering package for the fabrication and installation of the damaged internal diffuser, internal duct, and a new bottom cone, all provided in complete sizes. The installation will be executed in three phases to ensure a maximum downtime of the conditioning tower of 48 h. Upon completion, the conditioning tower will be restored to its standard condition. Our commitment to the client and our facilities remains of paramount importance to us.
Support
Danieli has consistently provided support when facing fire and draught issues caused by tar build-up resulting from bad pitch burning, as well as to reduce baking time to increase anode production. A specialized team offers remote assistance and on-site support when needed. Additionally, Danieli offers surveys where the entire FTC is inspected, fine-tuned, and operators are advised on how to manage problems and maintenance effectively. We also provide training for operators and maintenance teams to ensure they understand the design, process, and various tips and tricks aimed at extending the operating life of the FTC. After each survey/inspection of an FTC, the defects are presented, and an action plan is developed. Additionally, spare parts are recommended and provided to carry out the repairs.
Conclusions
The production of anodes for aluminium smelting comes associated with the emission of multiple pollutants, such as hydrofluoric acid (HF) and polyaromatic hydrocarbons (PAH). Given the nature of the anode baking process, fumes are also prone to show temperature spikes/sparks and contain tar/sticky matter. Changes in the sulphur content of the used pet coke have led to a rise in sulphuric emission (SO2, SO3, H2SO4) while capacity creep at potlines and the associated baking furnaces have stretched many fume treatment centers towards or beyond the limits of their design capacities.
The “Pleno” design for dry scrubbing of anode baking furnace fumes and potline gases was developed in the 1980s with the objectives of robustness and maintenance friendliness. All of the “Pleno” design FTCs and GTCs that have been decommissioned, were taken out of operation for business reasons rather than technical. These units have demonstrated their ability to remove pollutants and cope with the aforementioned temperature spikes and sparks.
One of the keys to a long lifetime is in the “dry bottom” operation of the conditioning tower,while the conditioning tower primarily serves to protect the baghouse modules, this operating mode also eliminates the risk of (acidic) corrosion downstream by preventing condensation and as such, acid-accelerated corrosion. “Dry bottom” operation is achieved by proper engineering of the conditioning tower and is maintained by effective maintenance of especially the spray lances. However, though lacking maintenance may jeopardize some equipment, operational experiences with “Pleno” design fume treatment centers have shown that even in those cases, the “Pleno” design FTC is robust will not fail.
References
- Stephan Broek, Ike Loukos, Smelters scrub up with Pleno IV, Aluminium Today, January/February issue (1999), 21–23.
- Peter Klut, Wouter Ewalts, Travis Turco, Aluminerie de Bécancour Conditioning Tower Replacement, Proceedings of the 145th TMS Annual Meeting, Nashville – TN, USA, 14–18 February 2016, 479–483.
- Erik Dupon, Edo Engel, Rick Oliana, Bas Admiraal, Peter Klut, Structured Approach to Modernization of Fume Treatment Centers, Proceedings of the 143rd TMS Annual Meeting, San Diego – CA, USA, 16–20 February 2014, 1181–1185.
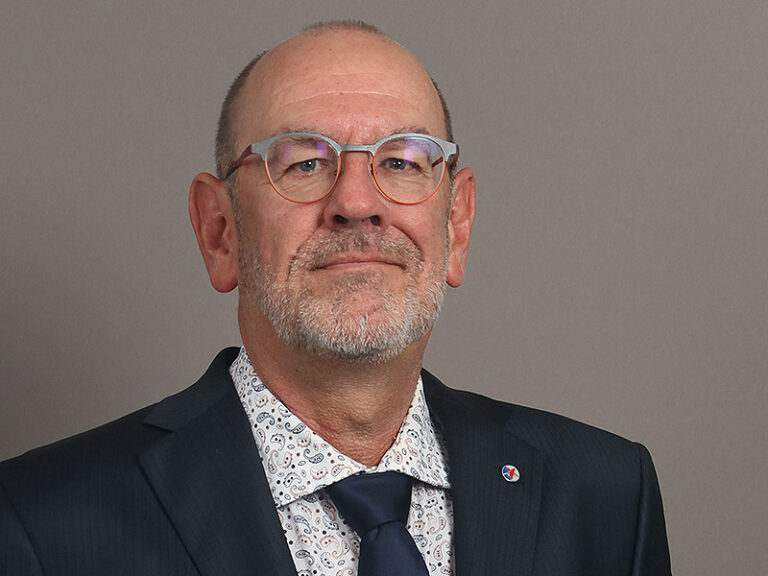
"*" indicates required fields